Ein Blick über die Grenzen - Eine neue Perspektive auf Asphaltproduktion
Ein Blick über die Grenzen - Eine neue Perspektive auf Asphaltproduktion
Eine ultimative Erfolgsgeschichte: Die perfekte technische Lösung trifft auf den idealen Geschäftsplan.
Oft betrachten wir nur die Erfahrungen in unserem eigenen Land und schauen nicht immer genau hin, was an anderen Standorten, in diesem Fall Madrid, passiert. Wir sagen uns: "Aber der Markt im Ausland ist anders. Das würde zu Hause nie funktionieren."
Vielleicht - aber auch jenseits unserer Grenzen werden Straßen mit Füllstoffen und Bitumen gebaut, genau wie bei uns. (In manchen Fällen werden sie sogar besser gebaut.) Das Mischgut wird in denselben Asphaltmischanlagen hergestellt, es sei denn, es müssen spezielle örtliche Regeln beachtet werden. In einigen Ländern wird beispielsweise eine kontinuierliche Mischanlage anstelle einer Chargenmischanlage verwendet. Selbst diese Unterschiede sind oft eher philosophischer als technischer Natur.
Alle Asphalthersteller, zumindest in Westeuropa, haben ähnliche Anforderungen. Dazu gehört der maximale Anteil von Recycling-Asphalt (RAP), um die Umwelt am wenigsten zu belasten wie auch die Rückgewinnung eines möglichst großen Teils des alten Bindemittels. Auch die Minimierung der Lärm- und Geruchsemissionen sind ein sehr wichtiger Aspekt.
Was die Unternehmen in den Nachbarländern voneinander unterscheidet, ist oft die Organisationsstruktur. Frankreich ist in diesem Bereich führend, da drei große Unternehmen mehr als 80 % der Asphaltproduktion unter sich aufteilen.
Diese Eigentumsverhältnisse führen dazu, dass immer mehr Anlagen von mehreren Unternehmen betrieben werden - sei es im Rahmen eines zeitlich begrenzten Konsortiums für ein Großprojekt oder im Rahmen eines laufenden Vertrags.
Diese Partnerschaften nutzen eine einzige größere Anlage an Stelle vieler kleinerer Produktionsstätten in einem Gebiet. Die gemeinschaftlich genutzte große Anlage ist in der Regel moderner und technologisch fortschrittlicher.
Die Vorteile dieses Ansatzes sind bedeutend.
Größere Produktionsmengen führen zu einer Senkung der Rohstoffkosten angesichts der hohen Abnahmemengen.
Die Effizienz der Anlage verringert den Materialabfall, was eine weitere wichtige Kosteneinsparung darstellt.
Die Fixkosten für Investition, Wartung und Personal der Anlage werden auf mehrere Eigentümer verteilt.
Die Wartung und der Austausch von Ersatzteilen können in einer großen Anlage schneller durchgeführt werden als in mehreren kleineren Anlagen.
Diese Vorteile führen zu zwei wesentlichen Ergebnissen:
Die Produktionskosten pro Tonne Asphalt werden gesenkt.
Weniger Anlagen in einem Gebiet wirken sich positiv auf die Umwelt aus. Denn die Emissionen einer einzigen größeren Anlage sind deutlich geringer als die mehrerer kleiner Anlagen.
Es gibt viele Gewinner, die von einem einzigen Betrieb profitieren, einschließlich der Wohngebiete, da weniger Einwohner in der Nähe einer Anlage leben.
Unser Beispiel: Madrid/Spanien
Mit diesen Überlegungen entstand das Projekt in Madrid. Lokale Asphalthersteller schlossen sich zu der International Construction Group zusammen.
Spaniens Hauptstadt hat mehr als 3 Millionen Einwohner, die umliegenden Gebiete nicht mitgerechnet. Das Straßennetz innerhalb der Stadtgrenzen erstreckt sich über Hunderte von Kilometern. Um die Auswirkungen des Verkehrs auf das Stadtgebiet zu minimieren, wurden häufig Tunnel gebaut.
Die Nachfrage nach Asphaltmischgut ist angesichts des ausgedehnten Straßennetzes groß. Ebenso wichtig ist jedoch die Notwendigkeit, die Zahl der Anlagen zu verringern, da gewisse Flächen mittlerweile für Wohnbebauung genutzt werden. Die Anlagen müssen jetzt an strategisch sinnvollen Standorten platziert werden. Die Zeiten, in denen eine Anlage, die 70.000 Tonnen Asphalt pro Jahr produziert, in einem städtischen Gebiet angesiedelt wird, sind vorbei.
Das Konsortium aus französischen und spanischen Bauunternehmen in Madrid entschied sich für die Ammann ABP 320 Universal Asphalt-Mischanlage. Sie überzeugte mit mehreren Vorteilen und Eigenschaften.
Die flexible Anlage kann in der Zukunft erweitert werden, um Änderungen und neuen Anforderungen gerecht zu werden. (Insbesondere kann sie um den Trockner RAH100 erweitert werden, der ausschließlich für die Erwärmung von RAP verwendet wird)
Dem Konsortium steht ab sofort die zweite Generation des RAH50 zur Verfügung, die über einen Recyclingring am Trocknerzylinder verfügt. Der RAH50 ermöglicht die Verwendung von bis zu 50 % RAP und reduziert die Emissionen erheblich.
Bis zu 40 % kaltes RAP kann über das Dosiersystem zugeführt werden. Zwei Materialbehälter können an der Spitze der Anlage untergebracht werden. Unabhängige Wiege- und Dosierbänder können sowohl heißes als auch kaltes Mischgut verarbeiten.
Durch die Zugabe von Schaumbitumen, Pigmenten und verschiedenen Zusatzstoffen kann eine breite Palette von technischen Mischungen hergestellt werden.
Die Anlage Ammann ABP 320 Universal ist mit einem Untersieb für Heißgut ausgestattet, in dem 200 Tonnen heißer Zuschlagstoffe nach Korngröße und Zuschlagstoffart (z.B. Kalkstein und Basalt) getrennt werden. Dank der extrem dicken 200-mm-Isolierung können die heißen Materialien viele Stunden lang gelagert werden.
Ein Silo für das fertige Produkt hat ein Fassungsvermögen von mehr als 400 Tonnen Mischgut und kann zwei getrennte Lkw-Beladelinien beschicken. Die Temperatur des Mischguts kann über viele Stunden aufrechterhalten werden, da das Silo ebenfalls mit einer 200 mm starken Isolierung ausgestattet ist. Das ist mehr als doppelt so dick wie der höchste Standard der Branche.
Darüber hinaus sorgt das Ammann as1 Control System für zusätzliche Effizienz. Es integriert alle Komponenten und reduziert den Abfall. Das System hat sich an vielfach weltweit bewährt und wird für seine fortschrittliche Technologie, intuitive Bedienung und Sicherheit geschätzt. Es überwacht Prozesse und kann in Zukunft um weitere Funktionen erweitert werden.
Einblick in den RAH50
In einer Branche, in der empirische Erkenntnisse und Gespräche auf der Baustelle die Produktentwicklung vorangetrieben haben, sind es nun innovative Daten und Simulationen, die diesen Prozess vorantreiben. Die Grundlagen haben ihre Berechtigung, werden aber am besten mit den heutzutage verfügbaren fortschrittlicheren Tools eingesetzt.
Das Endergebnis ist ein neuer Trocknerzylinder, der mechanisch bis zu 50 % recycelbare Stoffe verarbeiten kann. Er bietet einen um 30 % höheren Energieeffizienzindex als ein herkömmlicher Zylinder. Dieses bestätigt die Tatsache, dass die Temperatur der aus dem Zylinder austretenden Dämpfe um mehr als 30° C niedriger ist als bei allen anderen Zylindern. Die gesamte Energie wird mit den Zuschlagstoffen ausgetauscht.
Durch die Verwendung spezieller Stahlsorten kann der RAH50 die Leistungserwartungen erfüllen und gleichzeitig eine unübertroffene Haltbarkeit aufweisen. Dank der perfekten Kombination aus Trockner und Brenner (ebenfalls von Ammann entwickelt und produziert) und dem patentierten System zur Einbringung von RAP sind die Emissionen extrem niedrig. Bei diesem Verfahren wird das RAP sanft und allmählich erhitzt, um eine Beschädigung des Bitumens zu vermeiden. Die langsame, schrittweise Erwärmung des RAH50 steht im Gegensatz zu der "gewaltsamen" Methode, die in anderen Produkten Anwendung findet. Es ist kein Zufall, dass in den letzten 10 Jahren Hunderte von RAH50-Einheiten weltweit verkauft wurden.
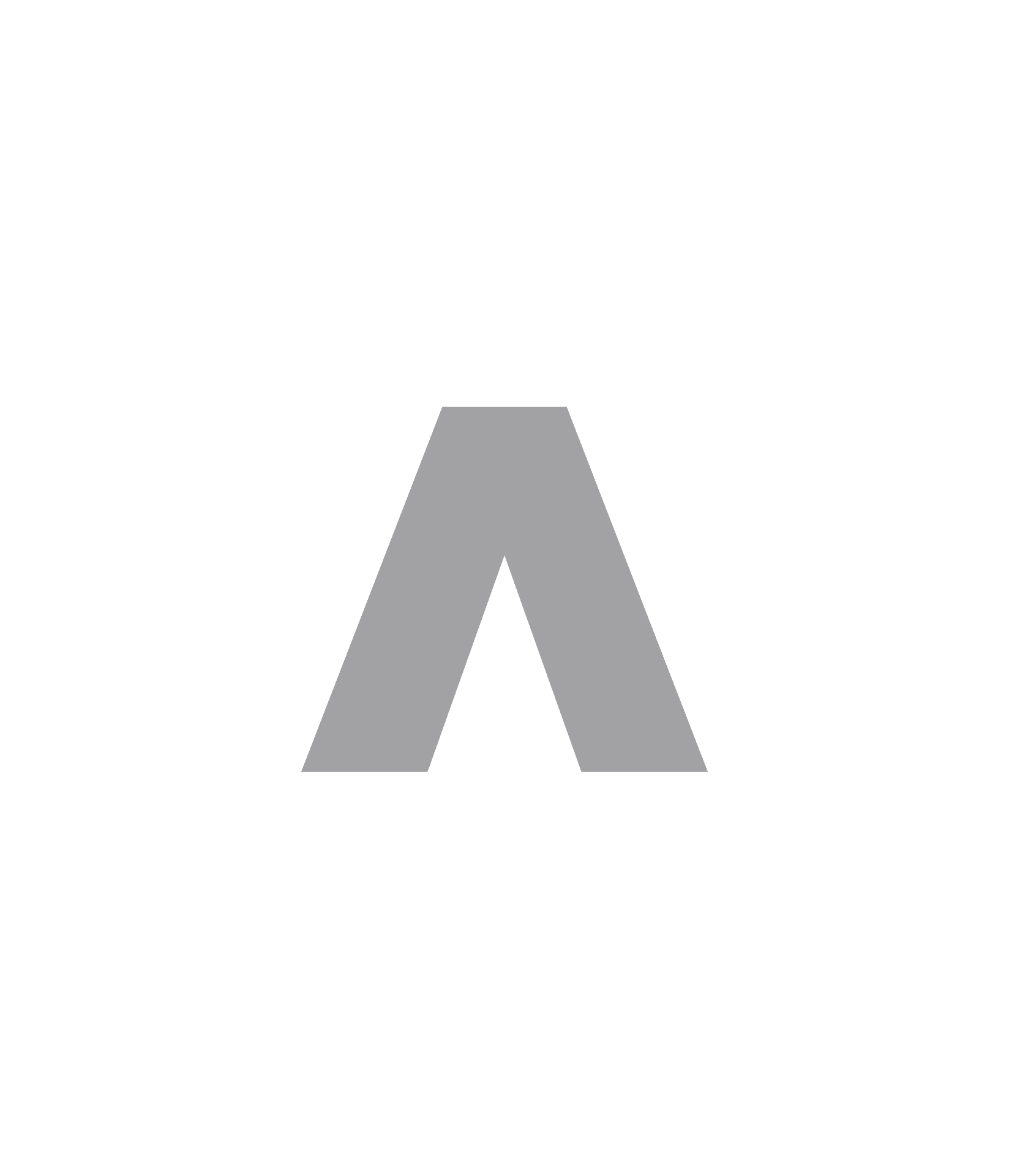
Kontakt-Formular
Online-Termin vereinbaren
Setzen Sie sich mit uns in Verbindung, um einen Vertriebsmitarbeiter in Ihrer Nähe zu treffen
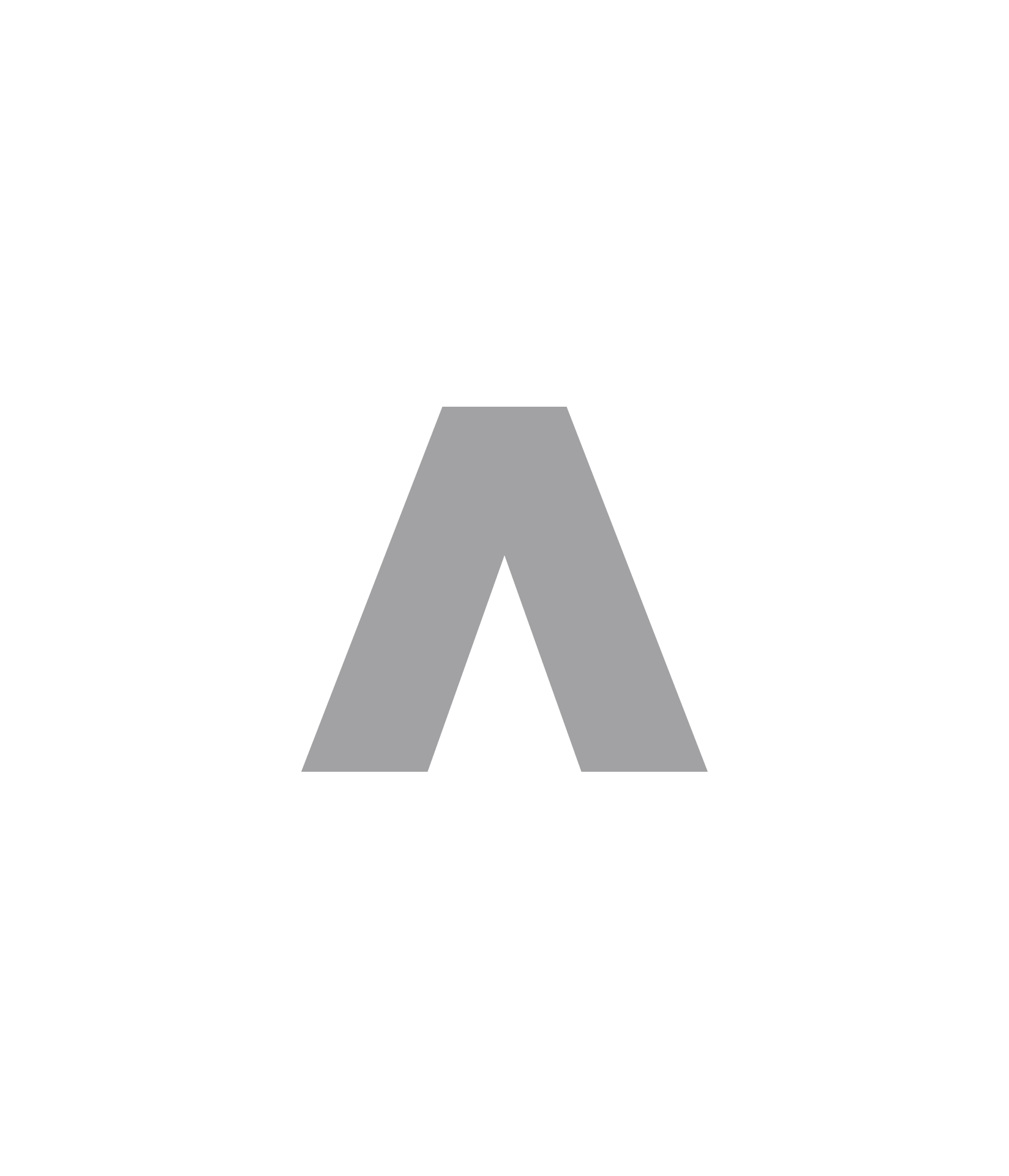