Soil and Asphalt Compactors
Ammann Expands Single Drum Roller Offerings
LANGENTHAL, Switzerland – Ammann has strengthened its line of single drum rollers with the launch of two compactors that serve the 15-ton and 17-ton weight categories.
The new Ammann ARS 150.1 T3 and Ammann ARS 170.1 T3 Single Drum Rollers are powered by highly reliable engines that meet EU Stage IIIA and U.S. EPA Tier 3 emissions standards. They replace the previous generation of ASC T3 compactors.
With this addition, Ammann now offers single drum compactors with the above emissions standards and weights ranging from 11 tons to 17 tons.
“The compaction power and manoeuvrability make these new rollers perfect fits for medium and large projects – including roads, highways and industrial areas,” said Radek Remes, Testing and Application Manager. “Control and operation are intuitive, which is especially beneficial for less experienced operators and those who provide training to newcomers.”
Reliable engines
The compactors serve the global market and can be placed in non-regulated markets, or markets that require EU Stage IIIA/U.S. EPA Tier 3 engines.
Both the Ammann ARS 150.1 and ARS 170.1 are equipped with proven and reliable Deutz diesel engines without any Engine After-Treatment (EAT) components. The absence of an EAT system simplifies service and maintenance while reducing ownership costs. Engine power output is 125 kW (168 hp) at 2200 RPM. These engines can run on high-sulphur fuels.
The powerful engines and high-pressure hydraulic system deliver excellent traction. A large fuel tank (310 litres) and low consumption ensure at least three working shifts without refuelling, reducing costs connected with logistics on the jobsites.
Compaction mastery
The ARS 150.1 and ARS 170.1 drums have a working width of 2130mm (83.9 inches). The four-bearing concept hosts two-stage vibratory mechanism. The ARS 150.1 generates eccentric forces of 325 kN at low frequency (29 Hz) and 237 kN at high frequency (35 Hz). The ARS 170.1 generates 335 kN and 260 kN at the same respective frequencies. The value of both amplitudes (1,9 mm high and 0,95 mm low) ensures excellent compaction throughout the depth of the layer.
The smooth drum, standard on both machines, has a thickness of 40 mm (1.6 inches), which lasts for the life of the rollers.
The compactors are available with an optional two-piece padfoot shell kit, which adds a tamping effect that is valuable when working with cohesive soils.
Ride and roll
The unique no-rear-axle concept makes the machines more compact, improving visibility and manoeuvrability. The design also allows the location of the engine to lower the centre of gravity, thereby enhancing stability, even when working on slopes.
A fully hydrostatic propulsion system makes traction a key differentiator. The drum and each wheel have their own drive motor and gearbox, optimising the traction forces necessary for safe operation in difficult terrains. Machines are equipped with a flow divider between the wheels (as standard) and can be upgraded with the Ammann Traction Control (ATC) system. ATC automatically controls power distribution between all three drive motors according to exactly defined ratios, further maximising traction.
A robust articulated joint provides consistent steering and riding. Oscillating frames ensure balanced weight distribution and consistent ground contact.
Operator first
The operating platform includes an integrated Roll-Over Protection Systems (ROPS). The platform is fully insulated and eliminates most vibration to the operator. This feature maximises comfort during the working shift, protects the operator’s health and increases jobsite safety.
Cab versions are extremely quiet and offer a wide range of advanced technical solutions, such as the elimination of A pillars. This significantly improves operator visibility to machine edges and surroundings. There is always 1-metre-by-1metre visibility in all directions for productive and safe operation. Windows on both sides of the cab can be opened and allow adjustment of rearview mirrors from the operator’s seat.
An adjustable steering column with multi-functional colored display provides status information such as working hours, fuel consumption and error codes. All control switches are located on the right armrest. Machine control is simple and intuitive; operators can learn to run the compactor in 10 minutes.
Ready for all applications
A wide range of optional equipment can boost the compactors’ productivity, comfort and safety. Options can be selected based on the customer’s requirements and jobsite needs.
The proprietary Ammann ACEforce (Ammann Compaction Expert) system is available. It enables easy monitoring of compaction progress for operators, improving effectiveness.
Serviceability
Serviceability, downtime and ownership costs are all addressed during research and development. Ammann teams from around the world collected information, and that input is reflected in the innovative design. In addition, the ECOdrop philosophy makes the machines maintenance friendly and environmentally focused.
The engine compartment is easily accessible, with a robust design that protects all major components. All maintenance and servicing points can be reached from the ground. The compactors are equipped with external draining points for essential fluids such as engine oil, cooling liquids and hydraulic oil.
When needed, onboard diagnostics facilitate quick troubleshooting.
The vibratory system is water-cooled and self-lubricated in an oil bath, reducing bearing maintenance and lowering operating costs.
ECOdrop philosophy
The rollers reflect a commitment to lower costs of ownership and maintenance. That includes reducing the volume of fluids required and making service points extremely accessible. This commitment – known as ECOdrop – makes all new products significantly more environmentally friendly.
With ECOdrop, fuel usage is 10% less when compared to the previous Tier 3 generation. The volume of required hydraulic oil has been reduced by 16%, while 38% less cooling liquid is required.
The new Ammann ARS 150.1 T3 and Ammann ARS 170.1 T3 Single Drum Rollers are powered by highly reliable engines that meet EU Stage IIIA and U.S. EPA Tier 3 emissions standards. They replace the previous generation of ASC T3 compactors.
With this addition, Ammann now offers single drum compactors with the above emissions standards and weights ranging from 11 tons to 17 tons.
“The compaction power and manoeuvrability make these new rollers perfect fits for medium and large projects – including roads, highways and industrial areas,” said Radek Remes, Testing and Application Manager. “Control and operation are intuitive, which is especially beneficial for less experienced operators and those who provide training to newcomers.”
Reliable engines
The compactors serve the global market and can be placed in non-regulated markets, or markets that require EU Stage IIIA/U.S. EPA Tier 3 engines.
Both the Ammann ARS 150.1 and ARS 170.1 are equipped with proven and reliable Deutz diesel engines without any Engine After-Treatment (EAT) components. The absence of an EAT system simplifies service and maintenance while reducing ownership costs. Engine power output is 125 kW (168 hp) at 2200 RPM. These engines can run on high-sulphur fuels.
The powerful engines and high-pressure hydraulic system deliver excellent traction. A large fuel tank (310 litres) and low consumption ensure at least three working shifts without refuelling, reducing costs connected with logistics on the jobsites.
Compaction mastery
The ARS 150.1 and ARS 170.1 drums have a working width of 2130mm (83.9 inches). The four-bearing concept hosts two-stage vibratory mechanism. The ARS 150.1 generates eccentric forces of 325 kN at low frequency (29 Hz) and 237 kN at high frequency (35 Hz). The ARS 170.1 generates 335 kN and 260 kN at the same respective frequencies. The value of both amplitudes (1,9 mm high and 0,95 mm low) ensures excellent compaction throughout the depth of the layer.
The smooth drum, standard on both machines, has a thickness of 40 mm (1.6 inches), which lasts for the life of the rollers.
The compactors are available with an optional two-piece padfoot shell kit, which adds a tamping effect that is valuable when working with cohesive soils.
Ride and roll
The unique no-rear-axle concept makes the machines more compact, improving visibility and manoeuvrability. The design also allows the location of the engine to lower the centre of gravity, thereby enhancing stability, even when working on slopes.
A fully hydrostatic propulsion system makes traction a key differentiator. The drum and each wheel have their own drive motor and gearbox, optimising the traction forces necessary for safe operation in difficult terrains. Machines are equipped with a flow divider between the wheels (as standard) and can be upgraded with the Ammann Traction Control (ATC) system. ATC automatically controls power distribution between all three drive motors according to exactly defined ratios, further maximising traction.
A robust articulated joint provides consistent steering and riding. Oscillating frames ensure balanced weight distribution and consistent ground contact.
Operator first
The operating platform includes an integrated Roll-Over Protection Systems (ROPS). The platform is fully insulated and eliminates most vibration to the operator. This feature maximises comfort during the working shift, protects the operator’s health and increases jobsite safety.
Cab versions are extremely quiet and offer a wide range of advanced technical solutions, such as the elimination of A pillars. This significantly improves operator visibility to machine edges and surroundings. There is always 1-metre-by-1metre visibility in all directions for productive and safe operation. Windows on both sides of the cab can be opened and allow adjustment of rearview mirrors from the operator’s seat.
An adjustable steering column with multi-functional colored display provides status information such as working hours, fuel consumption and error codes. All control switches are located on the right armrest. Machine control is simple and intuitive; operators can learn to run the compactor in 10 minutes.
Ready for all applications
A wide range of optional equipment can boost the compactors’ productivity, comfort and safety. Options can be selected based on the customer’s requirements and jobsite needs.
The proprietary Ammann ACEforce (Ammann Compaction Expert) system is available. It enables easy monitoring of compaction progress for operators, improving effectiveness.
Serviceability
Serviceability, downtime and ownership costs are all addressed during research and development. Ammann teams from around the world collected information, and that input is reflected in the innovative design. In addition, the ECOdrop philosophy makes the machines maintenance friendly and environmentally focused.
The engine compartment is easily accessible, with a robust design that protects all major components. All maintenance and servicing points can be reached from the ground. The compactors are equipped with external draining points for essential fluids such as engine oil, cooling liquids and hydraulic oil.
When needed, onboard diagnostics facilitate quick troubleshooting.
The vibratory system is water-cooled and self-lubricated in an oil bath, reducing bearing maintenance and lowering operating costs.
ECOdrop philosophy
The rollers reflect a commitment to lower costs of ownership and maintenance. That includes reducing the volume of fluids required and making service points extremely accessible. This commitment – known as ECOdrop – makes all new products significantly more environmentally friendly.
With ECOdrop, fuel usage is 10% less when compared to the previous Tier 3 generation. The volume of required hydraulic oil has been reduced by 16%, while 38% less cooling liquid is required.
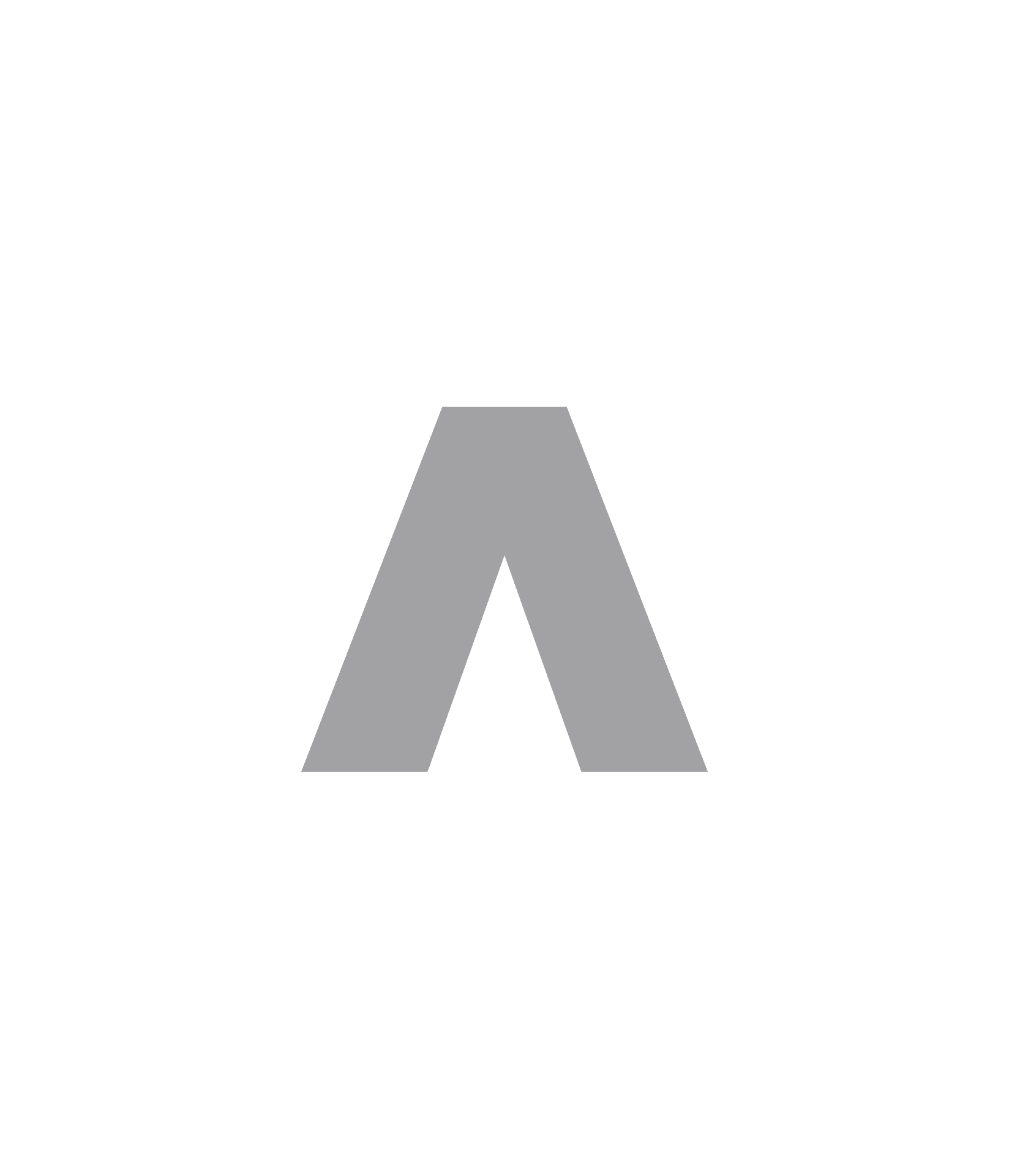
Contact Form
Schedule online meeting
Get in touch with us to meet a sales representative near you
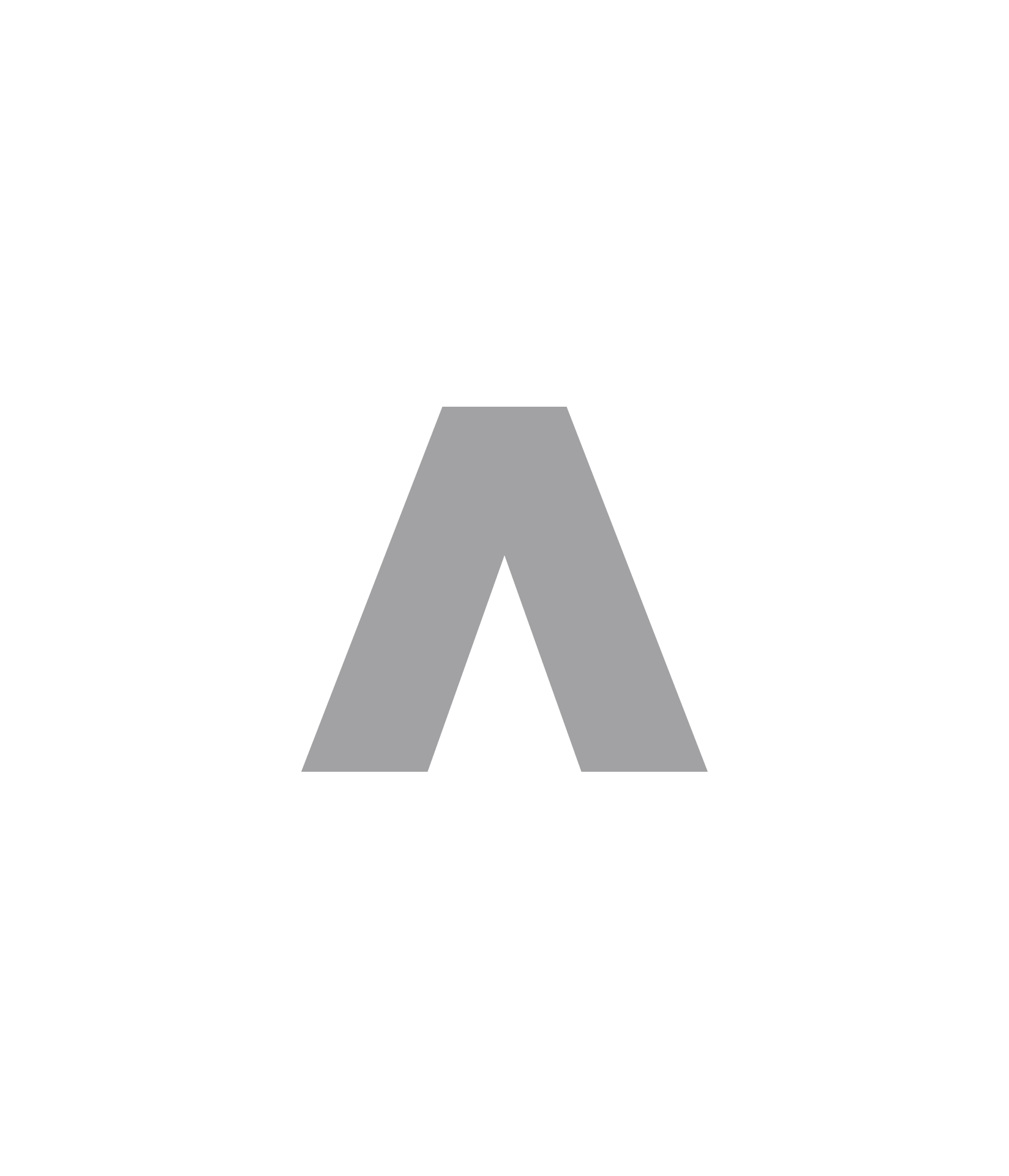