Latest Technologies and Innovations
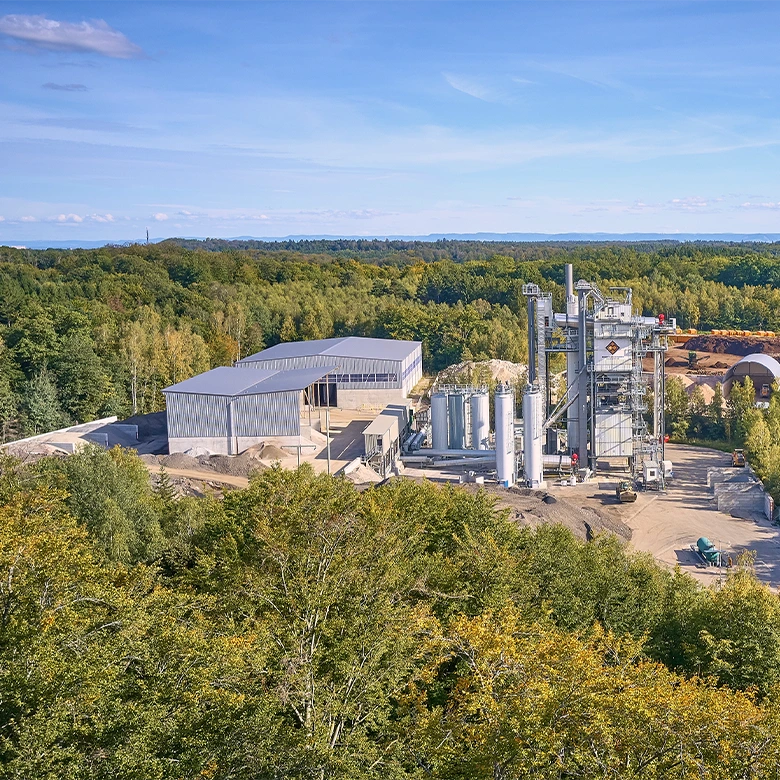
How can we use less, and how can we make what we do use last longer? These questions are at the core of Ammann’s sustainable efforts.
We pore over our existing plants, machines and processes in search of improvements, no matter how small they may seem. After all, incremental steps add up – a lesson we’ve learned over our more than 150 years in business.
What has this commitment brought? We’ve reduced emissions across all plants and machines, lessened fluid disposal needs and dramatically upgraded asphalt recycling capabilities – among other advances.