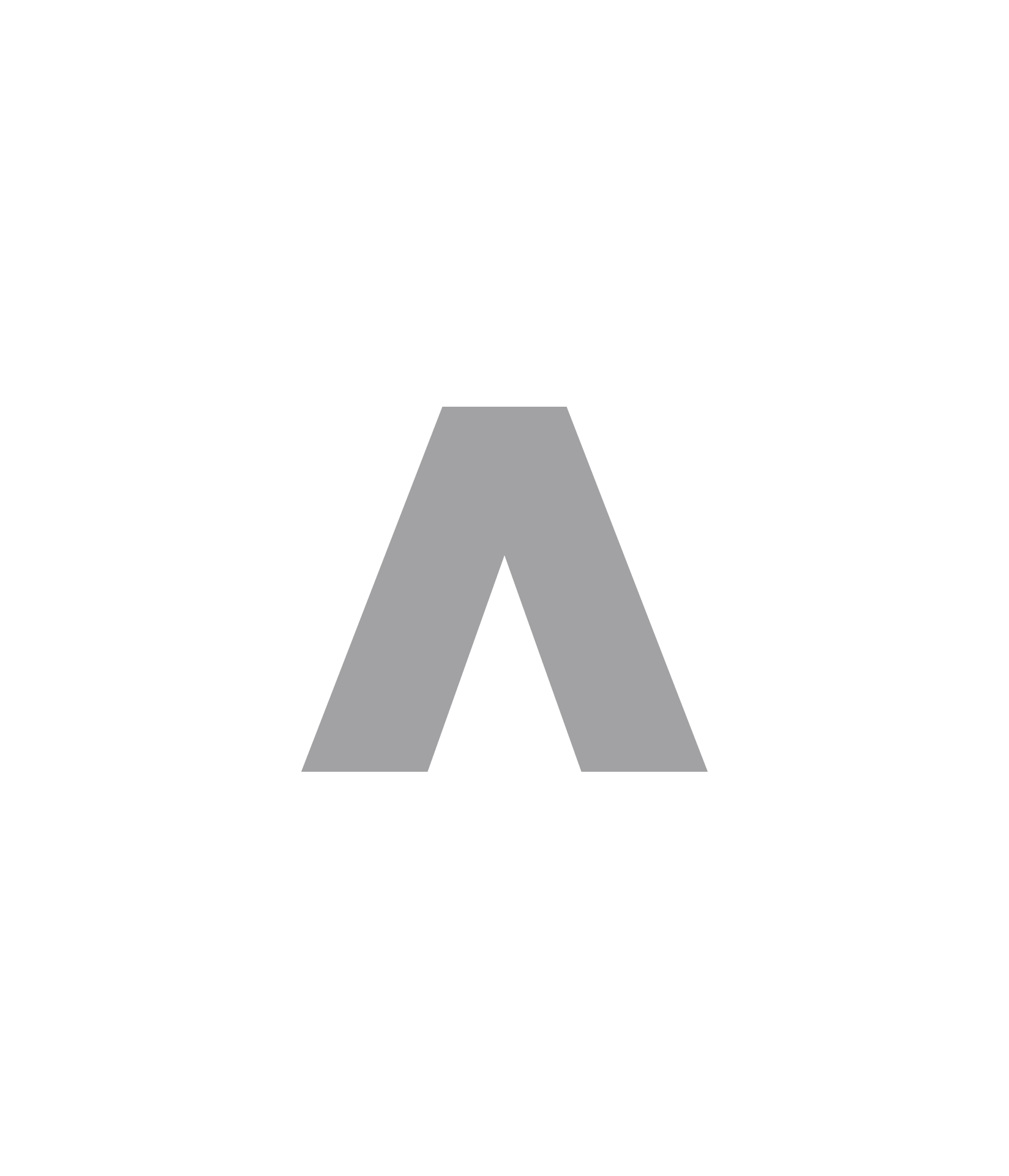
Ammann’s Commitment Connects with bauma 2025 Themes
The many gains in sustainability across Ammann’s product line are perfectly aligned with bauma 2025, to be held in Munich from 7-13 April.
“This is the leading trade fair for construction and roadbuilding equipment, and it is focused on key areas that Ammann also sees as essential to the future of the industry,” said Hans-Christian Schneider, CEO of Ammann.
Major bauma 2025 themes have been identified as climate neutrality, alternative drive concepts, networked construction and sustainable construction.
“These initiatives are reflected across Ammann, from light and heavy compaction, to paving, to the production of asphalt and concrete,” Schneider said. “Ammann’s commitment also includes retrofits of older equipment, which brings plants and machines up to modern sustainable standards. And of course there is the industry-leading technology that reduces emissions and enables the use of alternative energy sources.”
The products, technologies, services and processes that Ammann will feature at bauma 2025 are detailed below.
ROADBUILDING TECHNOLOGIES
The Connected Worksite
This is a smart technology that impacts all phases of roadbuilding. Smart technologies for the production and placement of asphalt are abundant, but they can be disjointed, too. Ammann’s digital solutions arrange all the puzzle pieces to create a single, clear image of the entire asphalt process. The result: improved sustainability and profitability.
Ammann and digitalisation expert Q Point jointly provide an integrated solution for all phases of the asphalt process. This combination improves efficiency, transparency and sustainability.
Autonomous Operation Cluster (AOC)
The first advances from Ammann’s participation in the Autonomous Operation Cluster (AOC) project will be featured at the show.
Now available on some Ammann heavy compactors is Birds-Eye View (BEV), a fully integrated camera system with a surround-view feature. This innovative system helps operators detect and avoid collisions with objects on the jobsite.
An additional operating feature is Safe Brake Assist (SBA), an active safety assistant system designed to prevent collisions on the jobsite.
ServiceLink
Ammann ServiceLink is a digital data management tool that provides customers with the information they want the most: machine location, battery status and hours. Data transfer is automatic thanks to new hardware, and access to the information is only a click away
This comprehensive fleet system provides key data for light compaction equipment, heavy compaction machines and asphalt pavers. Customers choose which machines to track. Equipment can be managed anytime, and from anywhere.
LIGHT COMPACTION EQUIPMENT
e-Drive Rammer
The Ammann eATR 68 Rammer delivers ground impact close to its petrol counterpart. Varied shoe shapes and sizes, including an asymmetric shoe for trench work, helps customise the rammer to the application. Shoes are easy to switch, too – all that’s required is the removal of four screws.
e-Drive Forward Moving Plate Compactors
Ammann offers four e-drive forward plates, as the new eAPF 15/40 and eAPF 15/50 join the previously released eAPF 12/40 and eAPF 12/50. The machines generate zero emissions. There are no fuel or oil filters to purchase or dispose of.
e-Drive Reversible Vibratory Plate Compactor
The newly released eAPR 20/40 is the first electric-drive reversible plate from Ammann. It is a great fit on small or confined worksites thanks to its light weight and narrow width. The ability to climb and overcome uneven terrain adds productivity in multiple applications.
An innovative handle concept lowers the hand-arm vibration (HAV) values to less than 2.5 m/sec², improving control and making work more comfortable and safer.
The e-drive rammers and forward and reverse plates share a common battery pack, charger and transport box. This allows a low battery to be swapped out with a fresh one from another machine. The batteries charge quickly – and hold their charge, too.
e-Drive Hydrostatic Vibratory Plate Compactor
The eAPH 70/95 electric-drive plate is powerful and heavy with a weight of 750 kg (1631 lb). As a zero emissions machine, the hydrostatic plate can work indoors and on the most highly regulated jobsites.
The electric drive requires less service than a combustible engine. There are no air filters and a very low volume of fluids. No tools are needed for daily maintenance. The eAPH 70/95 is powered by a lithium-ion battery, the LiFePo4 9.2 kWh.
APA Add-On Compactors
Two new add-on compactors, the APA 90/110 and the APA 110/110, reach locations that are unsafe for machines and operators, including steep slopes and trenches. They provide high compaction power and quickly process multiple material types.
These two APA Add-On Compactors are built for the 12-tonne to 40-tonne excavator class and for applications where a strong compaction performance is required. Layers as thick as 1 metre can be compacted, providing significant time savings when compared to traditional vibratory plates.
ARR 1575-2 Trench Roller
Ammann’s new slimmed-down trench roller is able to fit into tighter spaces and move more freely upon arrival at the jobsite.The ARR 1575-2 Trench Roller has a width of 600 mm (23.6 inches), compared with the previous 640 mm (25.2 inches).
An additional manoeuvrability factor, beyond the narrower frame, is a central steering joint with oscillation and two hydraulic cylinders that distribute force equally across the machine. This makes steering precise and smooth in both directions.
Another essential element is the two-stage vibratory mechanism, equipped with adjustable eccentric weights, that allows the operator to choose settings based on materials and depth.
ARW 65-S Walk-Behind Roller
An innovative pivoting mechanism enables the machine to move forward, backward and laterally.
The effortless lateral movement is a unique and significant advantage. Body weight is not required to direct the machine, which prevents operator fatigue, eliminates surface irregularities and provides consistency throughout the shift.
The 0.3 mm (0.01 inch) high amplitude setting makes the walk-behind roller ideal for compacting soil and substructures. The operator can switch to a lower amplitude of 0.15 mm (0.005 inch) when compacting asphalt and bitumen.
HEAVY COMPACTION EQUIPMENT
eARX 26-2 Light Tandem Roller
The roller features a fully electric drive that can operate for up to 10 hours without recharging. While categorised as a “light” machine, the compactor has an operating weight of 2640 kg (5820 lb). “To have a fully electric machine of this size is a breakthrough,” said Vlasta Medek, Commercial Management Heavy Compaction.
Because there is not a combustion engine, the eARX 26-2 is extremely quiet during operation. Sound levels reaching the operator station are 46% less than a diesel version.
The innovative powertrain concept eliminates almost all hydraulic components. The ecological impact is also lessened – and total ownership costs are significantly reduced – by replacing the diesel engine and its cooling system.
Key is the advanced 48-volt battery pack with a capacity of 600 Ah (31,5 kWh). The pack’s LiFePO4 technology is unique because each internal battery cell is independently protected so the entire pack is flame-resistant, increasing safety.
Ammann ARP 75 Pivot Steer Roller with Bird's-Eye View and Safe Brake Assist
Ammann has unveiled the Autonomous Operating Cluster (AOC) system, the latest advance in operator-focused technology and assistance.
The Bird’s-Eye View (BEV) includes a fully integrated camera system with a surround-view feature. This innovative system is seamlessly built into the HMI display, which rotates with the operator’s seat – offering unmatched usability and visibility compared to competitors. The solution also includes an optional trajectory overlay, delivering guidance to streamline machine operation.
An additional operating feature is the Safe Brake Assist (SBA), an active safety assistant designed to prevent collisions and accidents, further enhancing safety on busy construction sites.
ARX 90-2 and ARX 110-2 Articulated Tandem Rollers
The machines were redesigned to be more compact while expanding sight lines to all drum surfaces and edges. The 360º visibility from the operator station establishes a new market standard. The symmetrical cab integrates four ROPS posts directly in the main structure and close to doors, rather than in the cab’s corners, for improved visibility.
The articulated tandem rollers employ the next generation of Human Machine Interface (HMI) that facilitates easy, efficient operation. One component of HMI is fingertip steering (FTS), which makes the rollers more operator friendly, comfortable and easy to control.
FTS replaces the traditional steering wheel and allows operators to keep both hands on the armrests for enhanced comfort and control. It also offers palm support that prevents fatigue and injuries from repetitive motions.
Single Drum Rollers
Ammann ARS Soil Compactors utilise the innovative no-rear-axle concept, which maximises visibility and balance.
Weights range from the ARS 30, with an operating weight of 3480 kg (7672 lb), to the ARS 220, with an operating weight of 21 930 kg (48,347 lb). Multiple vibratory settings enable precise compaction on varied materials.
A reconfigured machine frame makes the most recent ARS models even more compact and better climbers, too. The ECOdrop system improves fuel consumption and lessens the amount of operational fluids needed.
ACEpro Intelligent Compaction System
Ammann has upgraded its advanced Intelligent Compaction system, ACEpro, to make it easier than ever for operators to access the built-in technology. The enhanced system has been integrated into Ammann ARP 75 and ARP 75 C Pivot-Steer Tandem Rollers.
Ammann Compaction Expert (ACE), the company’s proprietary automatic measurement, control and documentation system, was first launched in 1998. Several options have been introduced since then for both soil and asphalt applications. The latest version of ACEpro automatically controls and adjusts amplitude and frequency.
ABG PAVERS
eABG 4820 Electric-Drive Paver
The new eABG 4820 Paver is currently the largest electric paver on the market. It recently placed 1200 tonnes of asphalt in a day, while at the same time reducing C02 emissions by 70%.
The paver utilises a Variomatic screed and works at widths up to 6.5 metres (21 feet). Paving output is 500 tonnes per hour and maximum paving speed is 20 metres (66 feet) per minute. The hopper has a capacity of 12.7 tonnes.
The tracked paver is a perfect match for jobsites with restrictions on sound and emissions. It has excelled on the placement of wear, binder and base courses on streets and parking lots.
The paver has enough battery power to last an entire shift, regardless of the geography or the type of paving.
VDTA-V Adjustable Double-Tamper Screed
ABG’s double-tamper screeds, unique to the market, now have another significant advantage: Stroke on the front tamper of the newly patented VDTA-V Screed can be steplessly adjusted by the operator while the paver is working.
Previously, front tamper stroke could only be modified manually, and doing so was time consuming. The paver had to be shut down and the process required some effort. Because of this, the paving team often did not make changes, even if they would have positively impacted the paving results.
The on-the-fly modifications are particularly helpful when working with low temperature asphalt (LTA), placing double layers of mix, and paving along curves and roundabouts.
ABG City Class Pavers
These machines are the ideal choice for urban roadwork and other small- to mid-sized projects. The tracked ABG 2820 ensures a firm grip on challenging terrain. The ABG 2870 is the most compact wheeled paver from Ammann and provides high mobility on the jobsite.
The pavers’ proprietary hydraulic system helps the 55-kW engines achieve an outsized performance. The result is everything needed in an urban machine: efficient power, lower emissions, quieter operation and reduced fuel consumption.
The compact pavers, with 9-tonne hopper capacities, are strong enough to push a feed truck. Yet they are small enough to share a transport trailer with a compactor.
ABG 5420
The ABG 5420 Paver is a midsize machine with the sophistication of much larger highway-class pavers. The paver is built for the Indian market and for exporting outside India.
The machine is renowned for its value, which is considerable given the low purchase and ownership costs. It brings an ideal blend of power, efficiency, traction and stability. A 101-kW Eicher CEV Stage V engine powers the pavers in the Indian market. A Stage T3 Deutz (Volvo) D4E engine with 96kW is utilised in export markets.
ABG Multi-Class Pavers
These mid-sized machines have advantages more commonly associated with larger counterparts, including an advanced control system. The pavers easily adjust to jobsites of various sizes, providing the high productivity needed one day and the manoeuvrability necessary the next.
When higher production is needed, the tracked ABG 6820 and wheeled ABG 6870 achieve superior results. Both pavers combine high performance with low fuel consumption and low noise emissions. They bring the output needed, yet remain intuitive, easy-to-control machines.
The ABG 6870 is the only paver in its class with true public road homologation for Germany, Switzerland and Austria.
ABG Highway Class Pavers
The ABG 7820 and ABG 8820 provide the ultimate in paving productivity. The wide widths, powerful engines and high-capacity hoppers ensure these pavers are capable of tackling the biggest jobs. The machines can place mats as thick as 300 mm (12 in).
The Ammann ABG 7820 offers high production, with an ability to pave as wide as 11 metres (36 feet). The durably designed paver combines control with productivity-enhancing features. It furnishes industry-leading quality, shift after shift, through intuitive controls, superb screed technology and unparalleled visibility.
The ABG 8820 is a big machine for big jobs. It displays exceptional operator comfort and is compatible with a range of high-performance screeds. This is a paver engineered to bring outstanding production, quality and uptime. The paver has a maximum paving width of 13 metres (42 feet). A hopper capacity of 14.7 tonnes and large conveyor tunnel enable paving outputs of 1100 tonnes per hour.
CONCRETE PLANT
CBS Elba Concrete-Mixing Plant
The plant is a stationary solution that incorporates superior performance, flexibility and sustainability. Engineered for medium- to high-capacity applications, it delivers exceptional results, producing up to 200 m³ of compacted fresh concrete per hour. Its modular design ensures adaptability to diverse customer needs, making it the perfect choice for ready-mix and other demanding concrete applications.
With advanced aggregate storage options – such as high-raised enclosed chambers for superior environmental protection – it sets a new standard in eco-friendly and efficient concrete production. Engineered for long-term durability and tailored to adapt to evolving industry needs, the plant is a future-proof solution for modern concrete applications.
ASPHALT-MIXING PLANTS, COMPONENTS AND PROCESSES
ACP ContiMix 2.0 Asphalt Continuous Plant
The plant incorporates the benefits of both batch and continuous plants. It can utilise up to 100% RAP with the RAH100 dryer, or up to 50% RAP with the RAH50 2nd Generation.
ACP ContiMix can produce cold, warm and hot asphalt mix, and it is exceptionally efficient thanks to Ammann’s advanced technology for dryers, filters and energy usage. The as1 Control System is intuitive and brings further efficiencies.
High Recycling Technology (HRT) Asphalt Batch Plant
This is a premium Ammann plant, with advanced technologies working in harmony to incorporate up to 100% RAP with extremely low energy consumption and emissions.
The double-drum system combines a virgin aggregate drum with either an RAH60 or RAH100 recycling drum. Indirect, gentle heating reduces fuel burn and emissions. Heat distribution is more homogenous, too, which prevents sticking – as does the vertical flow.
The HRT is engineered to seamlessly integrate new, future technologies.
ABC SolidBatch Asphalt Batch Plant
This is a robust, reliable, high-production plant that requires a low initial investment. The plant can use up to 40% cold RAP in the mixer. Another option is the brand-new RAH35, which has a drum dryer with a ring for RAP. The RAH35 is presented for the first time at bauma 2025.
The plant is intended for customers who need to deliver results under tight deadlines. With its lowest cost of ownership, it represents the best value on the market. It also can be easily retrofitted with the latest Ammann technologies.
ABA UniBatch Asphalt Batch Plant
Maximum customisation, flexibility and performance are key benefits of the ABA UniBatch. The plant offers a range of production from 140-400 tons per hour, and the variety of configurations ensure customers can specify what they need. All components are perfectly integrated and designed to reduce fuel burn and emissions.
Ammann’s advanced RAP technologies enable the production of cold, hot and warm asphalt. Mix comprised of 100% RAP is possible. ABA UniBatch is “future optimised” and includes features that can be easily retrofitted so the plant always has the latest, most technologically advanced and profitable options.
ACM Prime 2.0 Continuous Mobile Asphalt Plant
Mobility and a smart continuous-flow process are hallmarks of this transport-optimised plant. Its compact design ensures the entire plant fits on one or two trailers, making relocation easy and efficient and complying with all international transport codes.
Components are tested at the factory and most are pre-assembled on the chassis, which saves a great deal of time when the plant reaches its destination.
The separated drying, heating and mixing processes result in high mix quality. A unique controllable outlet gate allows the filling height (and therefore the mixing time) to be set depending on the recipe and output.
Prime 2.0 is able to produce up to 210 tons per hour and use up to 40% cold RAP.
RAH35 Drying Drum
This is the latest recycling technology introduced by Ammann for its classic plants.
The RAH35 dryer utilises a recycling ring designed to incorporate up to 35% RAP. The dryer can be equipped on any plant and requires a minimal investment. A special ring enables introduction of RAP into the most suitable area of the cylinder. The dryer protects RAP from high temperatures and releases very low levels of emissions.
The RAH35 is available with a new generation long-nozzle Ammann burner, which allows introduction of RAP behind the flame. This further protects the RAP and lowers emissions.
RAH50 2nd Generation Drying Drum
Special types of steel provide high performance standards and unparalleled durability for this dryer, capable of handling up to 50% recycled material. The dryer is over 20% more energy efficient than a traditional cylinder, and emissions are very low thanks to the perfect pairing of the burner and cylinder – and Ammann’s patented system for gently heating RAP.
All these factors help explain how more than 250 units have been sold worldwide in the past 10 years.
RAH60 and RAH100 Drying Drums
These advanced recycling systems are able to utilise up 60% RAP and 100% RAP, respectively.
Both technologies are the subject of continuous and constant improvement, which includes design optimisation for further efficiencies: material usage; reduced maintenance and cleaning requirements; and the capability to utilise materials with increasingly high performances.
The systems recognize that temperature is a key factor when incorporating RAP. The recycled material must reach the target temperature, but it is imperative that it be heated gently so the bitumen isn’t damaged.
With the RAH60, RAP is heated in a traditional parallel flow dryer drum but at a lower temperature to protect the bitumen. Then, in a second dryer, virgin aggregate is heated to high temperatures. The aggregate exits that dryer and is mixed with the RAP, heating it in the process.
The RAH100 dryer consists of two connected sections. The first is a high technology, static, hot-gas generator. The generator creates the hot air, which is then transferred into the rotating second cylinder, consisting of a counterflow dryer.
The RAP enters the far end of the counterflow dryer but drops out before entering the hot gas generator. The RAP is never heated to temperatures that can damage it, the emissions are always very low, and there is almost no need to overheat the virgin aggregates.
The RAH100 is consistently confirmed as the best RAP usage technology on the global market.
Ammann Foam®
Ammann Foam® technology creates foam bitumen by injecting cold water into hot bitumen under high pressure, allowing for asphalt production at lower temperatures without chemical additives.
The equipment has been further improved and the generation process optimised. This allows customers to benefit from the best technology on the market and to meet the increasingly stringent regulations for emissions and CO2 abatement.
The advantages of this technology include reduced energy needs, lower emissions, better recycling, higher efficiencies at multiple stages of the process, improved compaction performance, an ability to transport mixes longer distances, and expansion of the paving season.
ENERGY SOURCES
MIBZ Wood Dust Burner
The Ammann MIBZ burner represents a revolutionary step forward in sustainable asphalt production, offering an eco-friendly alternative to traditional fossil fuel burners. By utilising renewable and CO₂-neutral wood dust as fuel, this innovative burner significantly reduces emissions while maintaining efficiency and reliability.
Over 50 asphalt plants globally have adopted this cutting-edge technology, producing more than 20 million tonnes of asphalt with wood dust and collectively reducing over 345,000 tonnes of CO₂ emissions. With this advancement, Ammann reinforces its leadership in providing sustainable and future-ready solutions for the asphalt industry.
H2 Burner
The Ammann H2 Burner is a groundbreaking solution for the asphalt industry, marking a new era in sustainability and efficiency. When using hydrogen, it eliminates CO2 emissions.
The new burner is engineered with multi-fuel technology, providing plant owners the ability to choose between hydrogen, natural gas and/or additional types of gaseous, liquid and dust fuels. Ammann’s advanced burner control enables easy switching between fuels, and mixed firings of different fuel types.
This advanced burner combines high performance with eco-consciousness, ensuring a seamless and efficient asphalt production process.
as1 Plant Control System V6.1
Process control and much more
With the latest as1 control system version 6.1, the unique, easy-to-use as1 control and management system platform for mix production is now available under Windows 11. The innovative Argon View user interface concept makes the operation of the system extremely simple, despite the comprehensive range of functions.
Another highlight are the various optional add-on modules to support production-related processes on the plant. In addition to the mobile applications such as the as1 PIP (Plant Information Point) or the as1 WLT (Wheel Loader Terminal), the new as1 PAA (Plant Asset App), a mobile solution for plant monitoring and for support in plant settings and troubleshooting, will be presented for the first time.
Now, as1 OPC UA Server (Open Platform Communications Unified Architecture), a standardized software interface in the industrial environment is supported. This allows the operating status of the system to be queried in real time and used for one's own evaluations. With the versatile possibilities in the field of statistics, reporting and data interfaces, your last open wishes will finally be fulfilled.
With the Ammann as1 control technology, you are investing in an innovative system with future-oriented technologies and globally proven process technology.
Hydrotreated Vegetable Oil (HVO)
HVO, a biofuel made from waste, has been approved for use in most Ammann diesel-burning machines. It is classified as a renewable diesel and renowned for having a longer shelf life than other biodiesels.
HVO reduces greenhouse gas emissions by up to 90% with no additional costs. Every 1000 litres of standard diesel fuel burned produces about 2640 kg of greenhouse gas CO2, compared to just 260 kg of greenhouse gas CO2 for every 1000 litres of HVO burned.
HVO-compatible Ammann machines require no engine modifications to burn the fuel. In addition, HVO provides the same performance as diesel fuel while slashing the amount of particulate matter released.
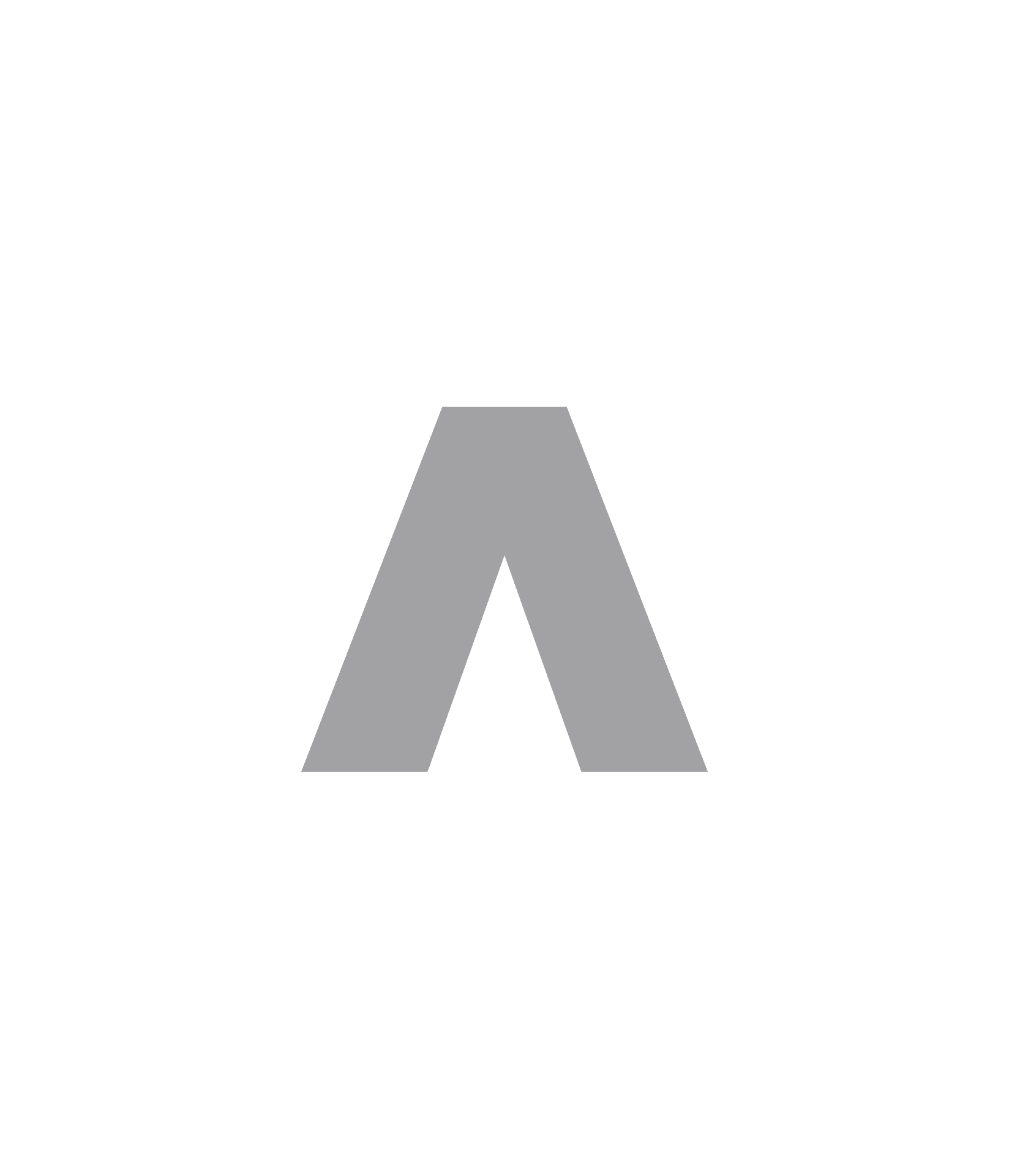
Contact Form
Schedule online meeting
Get in touch with us to meet a sales representative near you
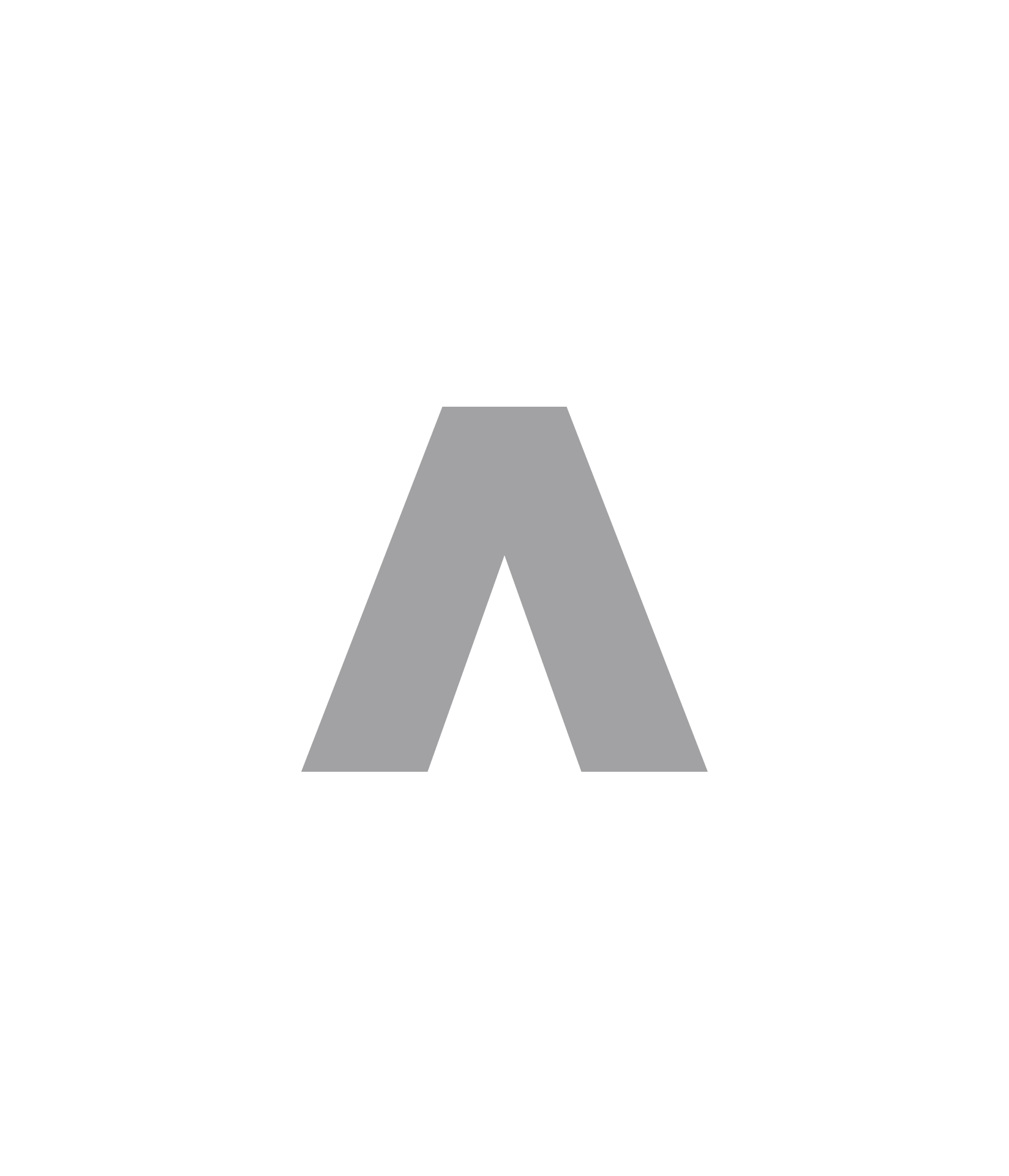