Asphalt Plants
Light Equipment
Soil and Asphalt Compactors
Asphalt Pavers
Technology
Shows and Events
Learn at Hillhead How Ammann Can Help Reduce Your Carbon Footprint – No Games Involved
LANGENTHAL, Switzerland – Ammann Group, a world-leading supplier of mixing plants, machines and services to the construction industry, is eager to explore its most recent advancements on the asphalt production sustainability front at Hillhead, the UK’s largest quarrying, construction and recycling exhibition.
The three-day event, slated for 25-27 June at Hillhead Quarry in Buxton, Derbyshire, will include indoor and outdoor exhibits as well as four areas demonstrating the latest equipment in a real quarry environment.
“Ammann is excited to return to Hillhead, and we’re looking forward to sharing our carbon reduction story with customers,” said David Hunt, Managing Director, Ammann U.K. “With the increasing global interest in environmental issues, we think the advantages offered by our Green Plant Initiative and electric-drive machines will really resonate with visitors who are interested in sustainable roadbuilding solutions.”
Asphalt-Mixing Plants
Ammann is deeply committed to providing the best, most sustainable technology to its customers. That dedication to customers has been the foundation of Ammann’s business for more than 150 years.
“We are a world leader in combustion technology for the asphalt industry,” said Martin van Stek, Commercial Manager - Plants at Ammann. “Every year we build more than 400 burners that are operating in countries all over the world.”
Hillhead will be an opportunity to discuss some of Ammann’s pioneering success in new green fuels such as tall oil, hydrogen and wood dust. “There are more than 40 plants equipped with wood dust burners, which have already produced more than 15 million tonnes of asphalt,” van Stek said.
Ammann has stayed ahead of adjustments in the market when it comes to alternative fuels. “We know what changes are coming, thanks to our longtime presence in the industry,” van Stek said. “If requirements, laws or regulations change, we act in advance. Many times, that means, ‘New rules, new fuels.’”
The Green Plant Initiative is Ammann’s renewed commitment to minimise or halt emissions at every stage of asphalt production. Among Ammann’s most significant emissions abatement technologies are burners that are CO2 friendly, and in some cases even neutral. Ammann provides burners for ecological solid fuels such as wood dust; for liquid fuels such as tall oil; and for gas fuels such as hydrogen – the cleanest of them all.
The H2 is an asphalt-mixing plant burner capable of utilising 100% hydrogen, which eliminates all CO2 emissions associated with the burner. The performance of the H2 is comparable to a fossil-fuel powered burner. Yet the H2 is easier to regulate, with better heat exchange in the dryer and an overall cleaner process.
Most Ammann gas burners currently on the market can use a combination of hydrogen and natural gas, but those configurations still lead to emissions. The versatile H2 is able to burn 100% hydrogen – and other fuels if desired. No adjustments are needed. Tall oil and wood dust are good options in areas where hydrogen can’t be sourced.
Ammann’s current burner control system enables a single burner to utilise four different fuels. Often times these fuels can be fired simultaneously. In addition, fuel changes can be made during production.
“Ammann experts will be on hand to explain how the H2 ecological fuel burners and the Ammann Foam system and other Ammann environmental solutions make asphalt production more climate friendly,” Hunt said.
Ammann Foam is engineered for maximum RAP utilisation and produces a warm mix with hot-mix properties. It slashes emissions while saving energy, achieving optimal quality with a minimal environmental footprint.
“There will also be opportunities to familiarize customers with the functions and benefits of the AS1 software system,” Hunt noted.
Ammann’s proprietary as1 Control System – the brains of the asphalt-mixing plant – can deliver an abundance of green improvements. It can increase mix quality while decreasing material usage and fuel consumption. It also gathers and processes key data to help uncover even more efficiencies. The as1 can be added to existing plants as a retrofit, resulting in immediate sustainability advancements.
Electric-Drive Machines
Ammann will spotlight several items from its lineup of electric-drive compaction equipment at Hillhead. These machines are powered by fast-charging, long-lasting batteries that pack the same punch as combustion engines – but with zero CO2 emissions. Power packs for light equipment are interchangeable, making it convenient to power other e-drive machines in your fleet.
The Ammann eATR 68 Rammer’s exceptional speed and torque control translate to more precise and efficient compaction. Operators are able to meet compaction targets quickly, limiting the amount of labor required. The electric-drive machine needs little maintenance, with no fuel or oil filters to purchase or dispose of.
Visitors seeking an e-drive plate that offers exceptional manoeuvrability and control need to look no further than the eAPF 12/40 Forward Moving Vibratory Plate Compactor. It delivers maximum vibratory frequency of 100 Hz – identical to its petrol counterpart. But because it’s battery powered, it is able to work indoors with poor ventilation and operate quietly in sound-sensitive jobsites, such as residential areas.
Its vibration-isolated handle reduces stress on the operator and can be folded and removed when working in confined areas or during transport. Operators also appreciate the easy-to-grip frame and single start/stop switch.
The eARX 26-2 Light Tandem Roller is a larger compactor, with a weight of 2640 kg and a drum width of 1200 mm. The roller features a fully electric drive that can operate for up to 8 hours without recharging. It is extremely quiet; sound levels reaching the operator station are 46% less than with a diesel version.
Its innovative powertrain concept removes almost all hydraulic components. The ecological impact is also lessened – and total ownership costs are significantly reduced – by replacing the diesel engine and its cooling system.
Mighty Mini Machines
Ammann will also feature a versatile mini paver and a small soil roller at Hillhead. The machines are so compact they can share a trailer to and from the jobsite.
Contractors praise the AFW 150-2 Mini Paver for its ability to work in areas as narrow as 250 mm, eliminating the time-consuming, difficult work of placing asphalt mix by hand. It is ideal in applications such as utility work, bike lanes, sidewalks and garden walkways. Yet it can pave up to 1650 mm when wider lifts are needed.
The compact machine has three wheels: two in the rear to enable traction and one in front for steering. Its tight turning radius enables performance in tight spaces and on sharp curves. It can be run by a single operator, and the fixed hopper can be side-loaded with a skid steer.
Ammann has recently introduced two small single-drum rollers, the Ammann ARS 30 and the Ammann ARS 50. The soil compactors utilise advanced technology, innovative engineering and robust engines to deliver high compaction output. They are the most compact rollers in Ammann’s soil compaction product line.
The ARS 30 and ARS 50 are ideal for road construction businesses and rental fleets that need a small, durable and powerful product for success on a daily basis. The rollers are suitable for compacting a wide range of materials and can be even more flexible given the smooth or padfoot drum options. Due to their compaction power and manoeuvrability, the machines are a good fit for small landscaping projects, forest roads, municipal roads and walking/bicycle paths.
“Ammann is proud to continue providing customers with innovative solutions to their roadbuilding challenges – solutions that are both sustainable and profitable,” Hunt said.
The three-day event, slated for 25-27 June at Hillhead Quarry in Buxton, Derbyshire, will include indoor and outdoor exhibits as well as four areas demonstrating the latest equipment in a real quarry environment.
“Ammann is excited to return to Hillhead, and we’re looking forward to sharing our carbon reduction story with customers,” said David Hunt, Managing Director, Ammann U.K. “With the increasing global interest in environmental issues, we think the advantages offered by our Green Plant Initiative and electric-drive machines will really resonate with visitors who are interested in sustainable roadbuilding solutions.”
Asphalt-Mixing Plants
Ammann is deeply committed to providing the best, most sustainable technology to its customers. That dedication to customers has been the foundation of Ammann’s business for more than 150 years.
“We are a world leader in combustion technology for the asphalt industry,” said Martin van Stek, Commercial Manager - Plants at Ammann. “Every year we build more than 400 burners that are operating in countries all over the world.”
Hillhead will be an opportunity to discuss some of Ammann’s pioneering success in new green fuels such as tall oil, hydrogen and wood dust. “There are more than 40 plants equipped with wood dust burners, which have already produced more than 15 million tonnes of asphalt,” van Stek said.
Ammann has stayed ahead of adjustments in the market when it comes to alternative fuels. “We know what changes are coming, thanks to our longtime presence in the industry,” van Stek said. “If requirements, laws or regulations change, we act in advance. Many times, that means, ‘New rules, new fuels.’”
The Green Plant Initiative is Ammann’s renewed commitment to minimise or halt emissions at every stage of asphalt production. Among Ammann’s most significant emissions abatement technologies are burners that are CO2 friendly, and in some cases even neutral. Ammann provides burners for ecological solid fuels such as wood dust; for liquid fuels such as tall oil; and for gas fuels such as hydrogen – the cleanest of them all.
The H2 is an asphalt-mixing plant burner capable of utilising 100% hydrogen, which eliminates all CO2 emissions associated with the burner. The performance of the H2 is comparable to a fossil-fuel powered burner. Yet the H2 is easier to regulate, with better heat exchange in the dryer and an overall cleaner process.
Most Ammann gas burners currently on the market can use a combination of hydrogen and natural gas, but those configurations still lead to emissions. The versatile H2 is able to burn 100% hydrogen – and other fuels if desired. No adjustments are needed. Tall oil and wood dust are good options in areas where hydrogen can’t be sourced.
Ammann’s current burner control system enables a single burner to utilise four different fuels. Often times these fuels can be fired simultaneously. In addition, fuel changes can be made during production.
“Ammann experts will be on hand to explain how the H2 ecological fuel burners and the Ammann Foam system and other Ammann environmental solutions make asphalt production more climate friendly,” Hunt said.
Ammann Foam is engineered for maximum RAP utilisation and produces a warm mix with hot-mix properties. It slashes emissions while saving energy, achieving optimal quality with a minimal environmental footprint.
“There will also be opportunities to familiarize customers with the functions and benefits of the AS1 software system,” Hunt noted.
Ammann’s proprietary as1 Control System – the brains of the asphalt-mixing plant – can deliver an abundance of green improvements. It can increase mix quality while decreasing material usage and fuel consumption. It also gathers and processes key data to help uncover even more efficiencies. The as1 can be added to existing plants as a retrofit, resulting in immediate sustainability advancements.
Electric-Drive Machines
Ammann will spotlight several items from its lineup of electric-drive compaction equipment at Hillhead. These machines are powered by fast-charging, long-lasting batteries that pack the same punch as combustion engines – but with zero CO2 emissions. Power packs for light equipment are interchangeable, making it convenient to power other e-drive machines in your fleet.
The Ammann eATR 68 Rammer’s exceptional speed and torque control translate to more precise and efficient compaction. Operators are able to meet compaction targets quickly, limiting the amount of labor required. The electric-drive machine needs little maintenance, with no fuel or oil filters to purchase or dispose of.
Visitors seeking an e-drive plate that offers exceptional manoeuvrability and control need to look no further than the eAPF 12/40 Forward Moving Vibratory Plate Compactor. It delivers maximum vibratory frequency of 100 Hz – identical to its petrol counterpart. But because it’s battery powered, it is able to work indoors with poor ventilation and operate quietly in sound-sensitive jobsites, such as residential areas.
Its vibration-isolated handle reduces stress on the operator and can be folded and removed when working in confined areas or during transport. Operators also appreciate the easy-to-grip frame and single start/stop switch.
The eARX 26-2 Light Tandem Roller is a larger compactor, with a weight of 2640 kg and a drum width of 1200 mm. The roller features a fully electric drive that can operate for up to 8 hours without recharging. It is extremely quiet; sound levels reaching the operator station are 46% less than with a diesel version.
Its innovative powertrain concept removes almost all hydraulic components. The ecological impact is also lessened – and total ownership costs are significantly reduced – by replacing the diesel engine and its cooling system.
Mighty Mini Machines
Ammann will also feature a versatile mini paver and a small soil roller at Hillhead. The machines are so compact they can share a trailer to and from the jobsite.
Contractors praise the AFW 150-2 Mini Paver for its ability to work in areas as narrow as 250 mm, eliminating the time-consuming, difficult work of placing asphalt mix by hand. It is ideal in applications such as utility work, bike lanes, sidewalks and garden walkways. Yet it can pave up to 1650 mm when wider lifts are needed.
The compact machine has three wheels: two in the rear to enable traction and one in front for steering. Its tight turning radius enables performance in tight spaces and on sharp curves. It can be run by a single operator, and the fixed hopper can be side-loaded with a skid steer.
Ammann has recently introduced two small single-drum rollers, the Ammann ARS 30 and the Ammann ARS 50. The soil compactors utilise advanced technology, innovative engineering and robust engines to deliver high compaction output. They are the most compact rollers in Ammann’s soil compaction product line.
The ARS 30 and ARS 50 are ideal for road construction businesses and rental fleets that need a small, durable and powerful product for success on a daily basis. The rollers are suitable for compacting a wide range of materials and can be even more flexible given the smooth or padfoot drum options. Due to their compaction power and manoeuvrability, the machines are a good fit for small landscaping projects, forest roads, municipal roads and walking/bicycle paths.
“Ammann is proud to continue providing customers with innovative solutions to their roadbuilding challenges – solutions that are both sustainable and profitable,” Hunt said.
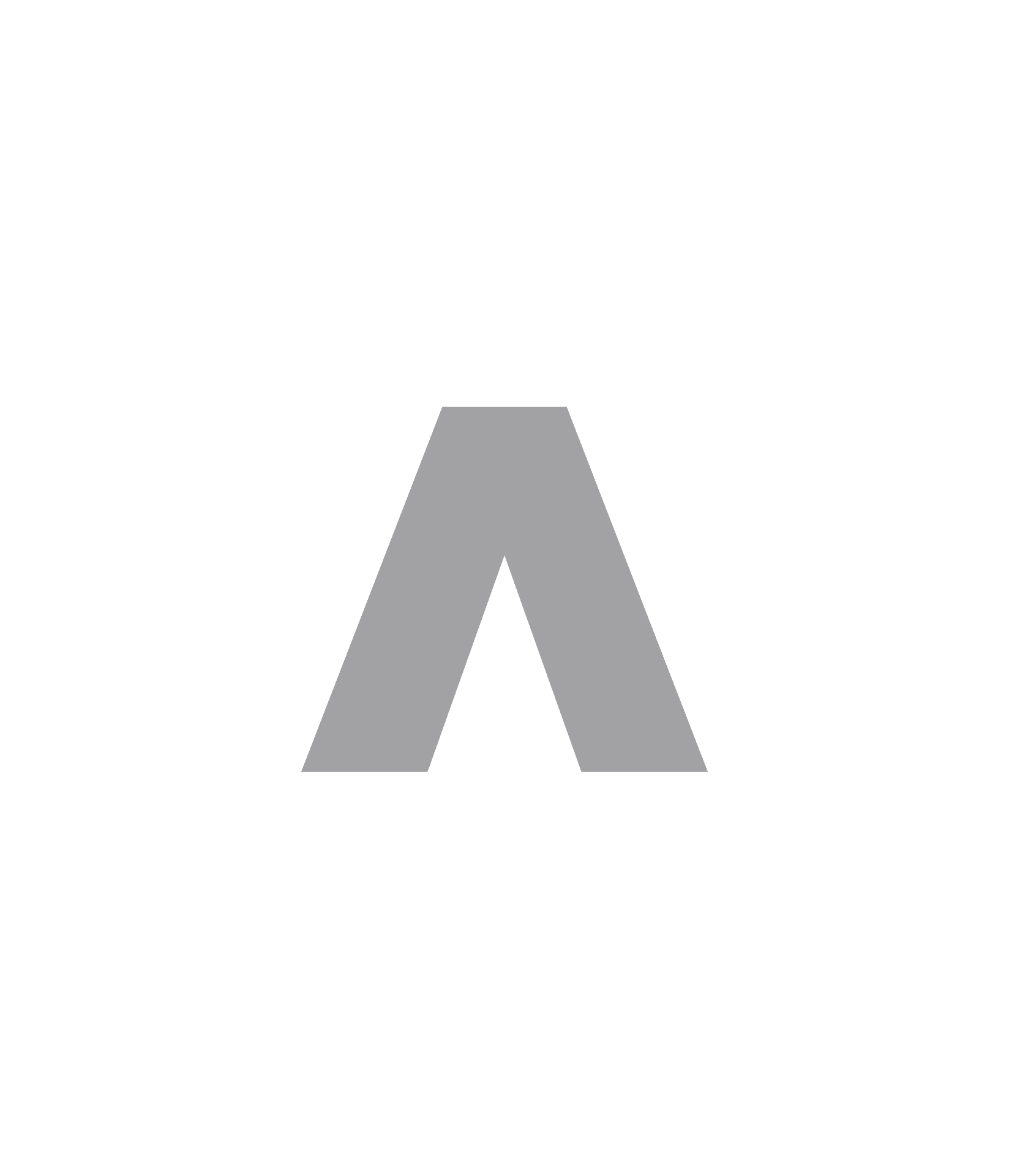
Contact Form
Schedule online meeting
Get in touch with us to meet a sales representative near you
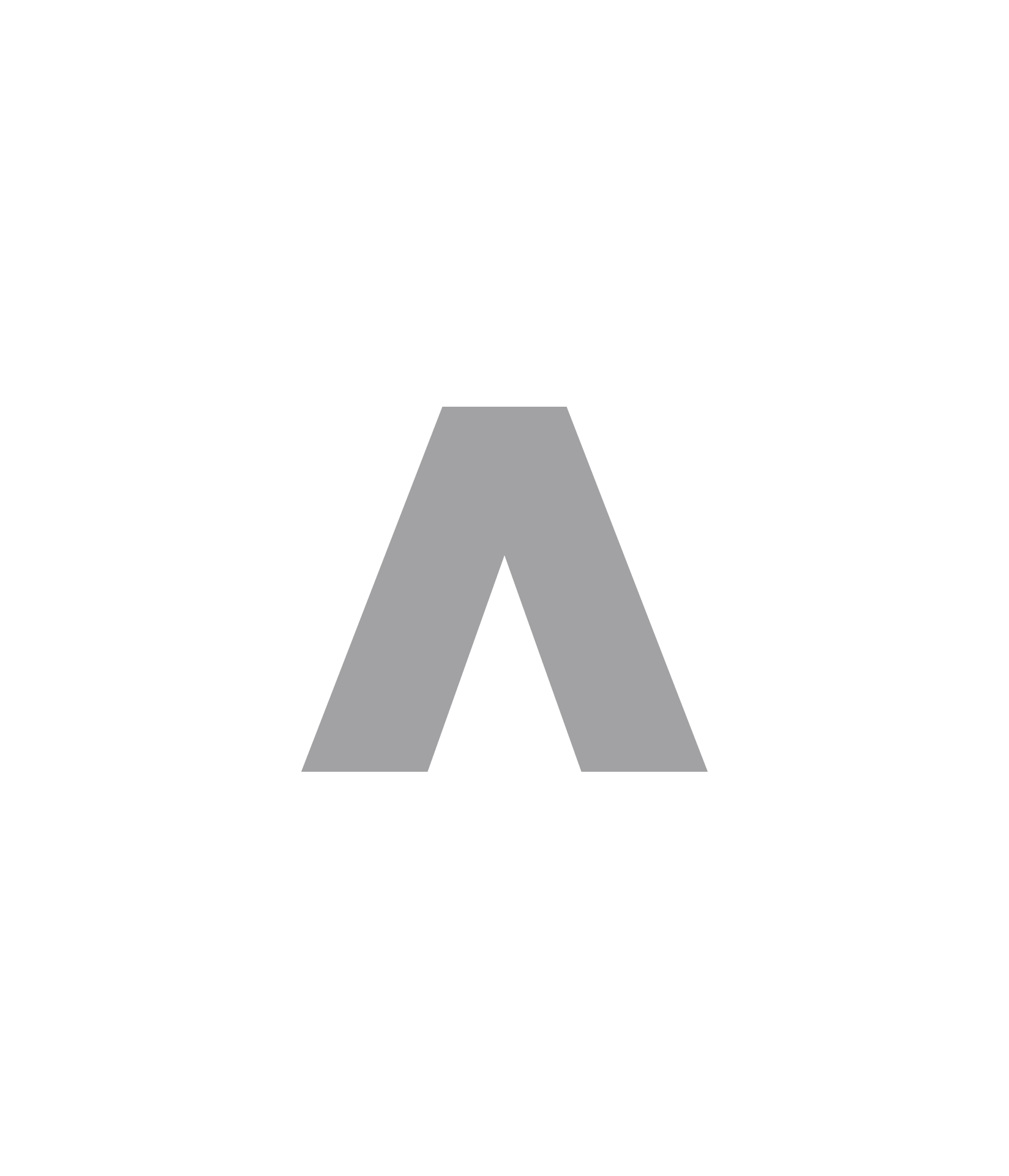