Una nueva perspectiva de la producción de asfalto a través de las fronteras
Una nueva perspectiva de la producción de asfalto a través de las fronteras
Es la historia de éxito definitiva: La solución técnica perfecta se encuentra con el plan de negocio ideal.
A menudo nos centramos en las experiencias de nuestro propio país y no siempre nos fijamos en lo que ocurre en otros lugares, en este caso Madrid. Nos decimos: "Pero el mercado es diferente en el extranjero. Nunca funcionaría en casa"
Tal vez. Sin embargo, fuera de nuestras fronteras, las carreteras se siguen construyendo con áridos de relleno y betún, igual que en casa. (La mezcla se produce en las mismas plantas mezcladoras de asfalto, a menos que se adapten a alguna preferencia local. Incluso estas diferencias suelen ser más filosóficas que técnicas. (Por ejemplo, algunos países utilizan una planta continua en lugar de una planta discontinua)
Todos los productores de asfalto, o al menos los de Europa Occidental, tienen necesidades similares. Una de ellas es maximizar el uso del asfalto reciclado (RAP) de forma que afecte lo menos posible al medio ambiente. Esto implica recuperar la mayor cantidad posible del antiguo ligante y, lo que es aún más importante, minimizar las emisiones. También es importante reducir el ruido y los olores.
Lo que distingue a las empresas de los países vecinos suele ser la estructura organizativa. Francia es el maestro en este ámbito, con tres grandes empresas que controlan (de una forma u otra) más del 80% de la producción de asfalto.
Estas estructuras de propiedad implican que cada vez más plantas son gestionadas por varias empresas o empresarios, quizá a través de un consorcio temporal para un gran proyecto o como parte de un acuerdo permanente.
Estas asociaciones suelen dar lugar a que una única planta más grande sustituya a muchas instalaciones de producción más pequeñas en el mismo territorio. La planta más grande es invariablemente más moderna y tecnológicamente avanzada que las que sustituye.
Las ventajas de este enfoque son significativas.
Una mayor producción conlleva una serie de beneficios, entre ellos una reducción del coste de las materias primas dado el elevado volumen que se adquiere.
La eficiencia de las plantas también reduce el desperdicio de material, otro ahorro de costes clave.
Los costes fijos relacionados con la compra de plantas, el mantenimiento y el personal se reparten entre varios propietarios.
El mantenimiento y la sustitución de piezas tienden a realizarse de forma más oportuna con una sola planta más grande que con varias instalaciones más pequeñas.
Estas ventajas generan dos resultados significativos:
Se reduce el coste por tonelada de producción.
La reducción del número de plantas en el territorio tiene un impacto medioambiental positivo, ya que las emisiones de una sola planta más grande son drásticamente inferiores a las emisiones combinadas de las plantas a las que sustituye.
Hay muchos ganadores, incluida una comunidad que se beneficia de una única operación, ya que menos residentes viven cerca de una planta.
El ejemplo de Madrid
Este es el contexto en el que nació el proyecto de Madrid. Los productores locales de asfalto unieron fuerzas con el mayor Grupo Internacional de Construcción.
La capital de España tiene más de 3 millones de habitantes, sin contar las zonas circundantes. Dentro de los límites de la ciudad existe una vasta red de carreteras que se extiende a lo largo de cientos de kilómetros. A menudo se utilizan túneles para minimizar el impacto urbano.
La demanda de aglomerado asfáltico es fuerte, dado el extenso sistema de carreteras. Sin embargo, es igualmente importante la necesidad de reducir el número de plantas, incluidas algunas situadas en lugares anteriormente aislados, donde los residentes se han expandido desde entonces. Ahora hay que situar las plantas en lugares más estratégicos. Los días en que una planta que produce 70.000 toneladas al año se situaba en un emplazamiento urbano ya no son la mejor solución.
La planta elegida por el consorcio liderado por una gran constructora franco-española en Madrid fue la Planta Universal de Mezclado de Asfalto ABP 320 de Ammann. Tiene varias características ganadoras que resultaron en su selección.
Se trata de una planta flexible que puede ampliarse en el futuro para adaptarse fácilmente a los cambios y nuevos requisitos. (En concreto, puede acomodar la posible adición del secador RAH100, que se utiliza exclusivamente para calentar RAP)
El consorcio dispone inmediatamente de la segunda generación del RAH50, con un anillo de reciclado en el cilindro del secador. El RAH50 permite utilizar hasta un 50% de RAP y reduce sustancialmente las emisiones.
Se puede introducir hasta un 40% de RAP frío a través del sistema de dosificación. Se pueden alojar dos tolvas en la parte superior de la planta. Las cintas independientes de pesaje y dosificación pueden manejar tanto mezclas calientes como frías.
Es posible producir una amplia gama de mezclas técnicas mediante la introducción de betún espumado, pigmentos y aditivos múltiples.
La planta Ammann ABP 320 Universal está equipada con una criba inferior de material caliente, en la que 200 toneladas de áridos calientes se separan por tamaños de grano y tipo de árido (piedra caliza y basalto, por ejemplo). Los materiales pueden almacenarse durante muchas horas, gracias a un aislamiento extremadamente grueso de 200 mm.
Un silo de producto acabado tiene una capacidad de más de 400 toneladas de mezcla y puede alimentar dos líneas separadas de carga de camiones. La temperatura de la mezcla puede mantenerse durante muchas horas porque el silo también está equipado con un aislamiento de 200 mm, más del doble del estándar más alto del mercado.
Además, el sistema de control as1 de Ammann añade eficiencia. Integra todos los componentes y reduce los residuos. El sistema ha demostrado su eficacia en cientos de emplazamientos de todo el mundo y es apreciado por su avanzada tecnología, su funcionamiento intuitivo y su seguridad. Supervisa los procesos y puede añadir más funciones en el futuro.
Visión del RAH50
En un sector en el que las pruebas empíricas y las conversaciones en el lugar de trabajo han impulsado el desarrollo de productos, los datos avanzados y la simulación impulsan ahora ese proceso. Aunque estos enfoques tienen su lugar, es mejor utilizarlos junto con las herramientas más avanzadas de las que disponemos actualmente.
El resultado final es un nuevo cilindro secador capaz de manipular mecánicamente hasta un 50% de materiales reciclables. Ofrece un índice de eficiencia energética un 30% superior al de un cilindro tradicional. Esto se confirma por el hecho de que la temperatura de los humos que salen del cilindro es más de 30° C inferior a la de cualquier otro cilindro, lo que demuestra que toda la energía se intercambia con los áridos.
El uso de aceros patentados permite a la RAH50 cumplir las expectativas de rendimiento manteniendo una durabilidad sin igual. Las emisiones son extremadamente bajas gracias a la perfecta combinación de cilindro secador-quemador (también diseñado y construido por Ammann) y al sistema patentado de introducción de RAP. El proceso consiste en calentar suave y gradualmente el RAP para evitar dañar el betún. El calentamiento lento y progresivo del RAH50 contrasta con el método más "violento" utilizado por otros productos. No es casualidad que en los últimos 10 años se hayan vendido cientos de unidades del RAH50 en todo el mundo.
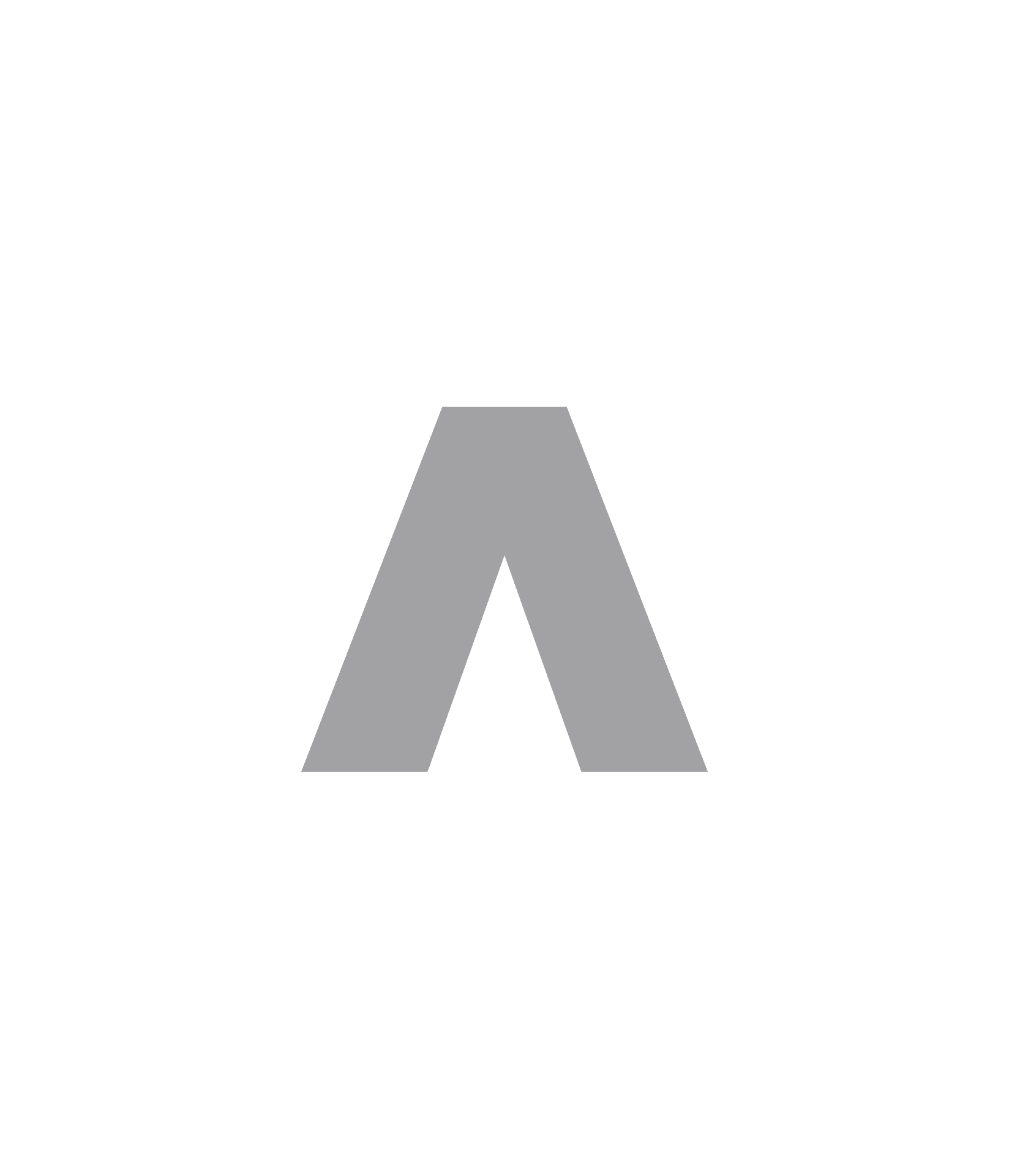
Formulario de contacto
Programe una reunión en línea
Póngase en contacto con nosotros para conocer a un representante de ventas cerca de usted
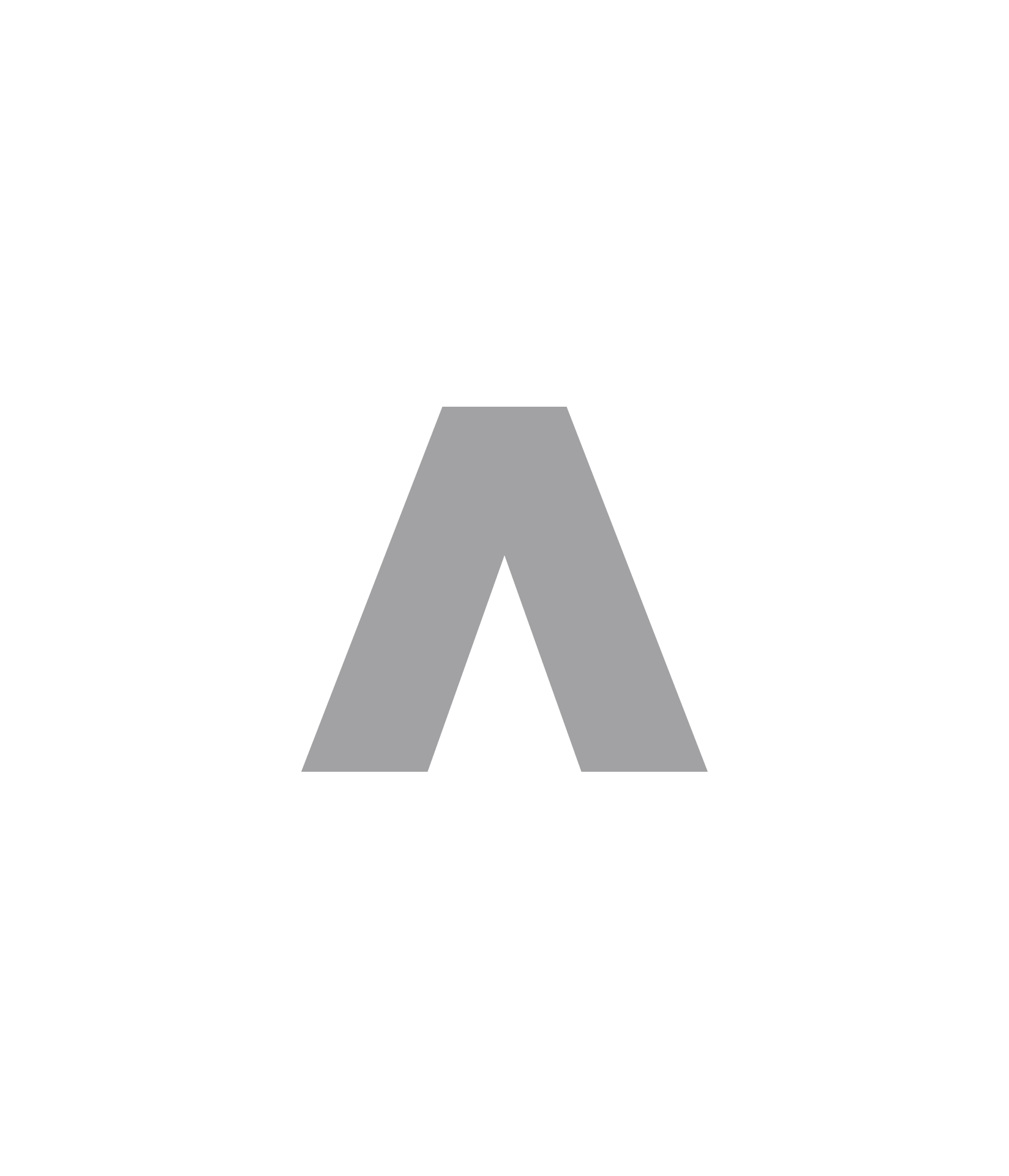