ABG Paver Outperforms Competitive Machine on LTA Jobsite
An ABG 7820 Paver with a VDT-V 79 screed had a strong performance in head-to-head testing against a competitive machine.
The ABG double-tamper screed provided 4% more pre-compaction, delivered more uniform temperature distribution, and was quieter than the competitor, which also worked with a high-compaction screed.
“The comparison proves that ABG Pavers bring an advantage to jobsites,” said Iwan Trompert, managing director of the BAM Infra Asphalt Company, which handled the paving. “In this case, ABG’s unique double-tamper system made a real difference. That level of pre-compaction makes it much easier for the crew to hit their subsequent numbers. This is even more essential when working with low-temperature asphalt (LTA).”
The jobsite
The paving occurred over two days in Nieuwerkerk aan den Ijssel in the Netherlands. BAM was in charge of the paving of the N219, a thoroughfare limited to motor vehicles.
The ABG 7820 worked parallel to the competitive model, with hot-on-hot, echelon paving. This ensured that both pavers placed the same type of asphalt mix under the same conditions.
The testing occurred on 1-2 October 2024.
Day 1
The machines, working in light rain, laid a binder layer with an approximate paving width of 3,5 metres each and a thickness of 8 cm. The mix was a low temperature asphalt (LTA) with foam bitumen as the binder. The asphalt was about 110º C when paving occurred.
LTA, also known as warm mix asphalt (WMA), is produced at lower temperatures, which reduces the amount of energy needed for heating, and therefore reduces emissions, too.
“It’s a process that makes paving more sustainable,” Trompert said. “It also means the compaction window is tighter. The double tamper helps crews meet that challenge.”
The crew at BAM wanted to test the pre-compaction effectiveness of the pavers when placing LTA. Both pavers worked with the same parameters: 1000 RPM tamper with vibration turned off. The paving speed was 4,5 metres per minute to start, and later increased to 6,5 metres per minute.
The results
A BAM employee regularly measured compaction with a Troxler probe.
The surface texture behind both machines was similar, but the testing showed the ABG 7820 and its VDT-V 79 screed achieved 4% more pre-compaction than the competitive model working under identical parameters. The BAM team also reported the ABG screed was significantly quieter.
Day 2
On the second day, conditions were cloudy but there was no rain as mix for the wearing course was placed at a thickness of 4 cm and a temperature of 150º C. The mix was an open porous asphalt (OPA), BBTM 5-A 70/100. The split mastics of the asphalt reduce traffic noise because openings in the texture partially absorb the sound.
As on Day 1, the parameters were identical – in this case, a tamper at 750 RPM with vibration turned off. The paving speed was 4,5 metres per minute.
The results
The surface textures behind both screeds were, again, the same. But measurements with an infrared camera showed more uniform temperature distribution behind the ABG 7820 with the VDT-V 79.
“A uniform temperature ensures consistent compaction later in the process,” Trompert said. “Such a benefit plays a role in subsequent steps, and ultimately promotes the success of the project.”
ABG screeds with this technology, including the VDT-V 79, offer optimal pre-compaction that reduces the number of compactor passes needed. Every pass that is eliminated lessens fuel burn, emissions and wear of the compactor.
The VDT-V 79 delivers a higher degree of compaction than a single tamper, in some cases as much as 7% more. In addition, an ability to reach up to 98% Marshall density dramatically reduces the number of necessary compaction passes.
As the name implies, double-tamper technology means the material is struck by two tampers. ABG screeds differentiate themselves by tamping the material twice before it reaches the screed baseplates.
The first tamper strikes the material in front of the screed, redistributing the mix as needed. The second tamper hits the mix again, also in front of the screed, assisting pre-compaction and further ensuring uniform density distribution, even with varying layer thickness.
The material is already pre-compacted and level before reaching the baseplates. Therefore, the baseplates simply provide the finishing touches that support exceptional pre-compaction and smoothness.
Double-tamper screeds have proven successful in a variety of applications. They include paving base, binder and wear courses; granular materials; roller-compacted concrete (RCC); and cement-bound materials (CBM).
The tampers, and the pre-compaction they bring, are also invaluable in applications where traditional compaction methods are difficult to conduct. Examples are the laying of asphalt-sealing surfaces on dam slopes, and on circuits with high banks for testing and racing.
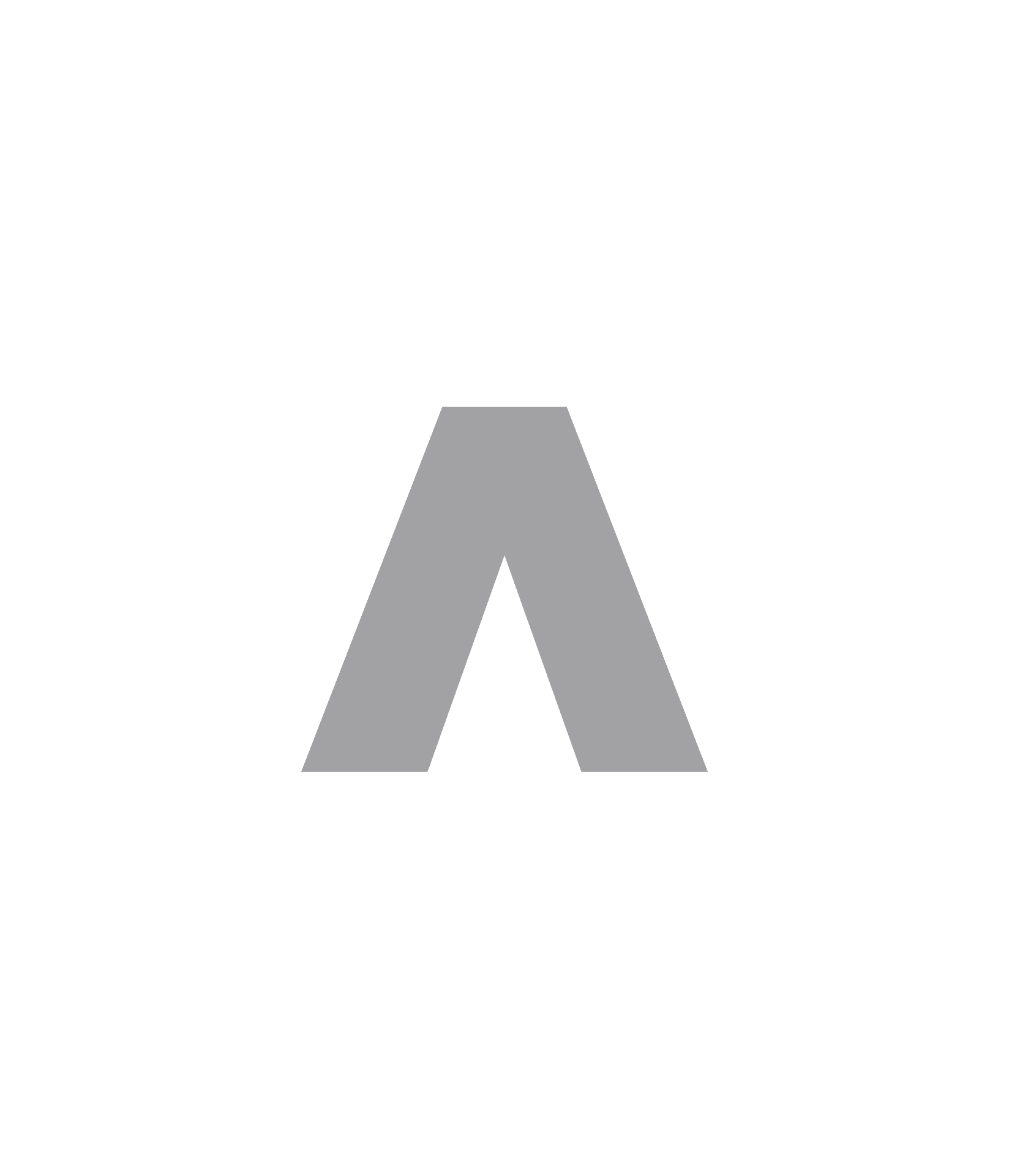
Formulaire de contact
Planifier une réunion en ligne
Prenez contact avec nous pour rencontrer un représentant commercial près de chez vous
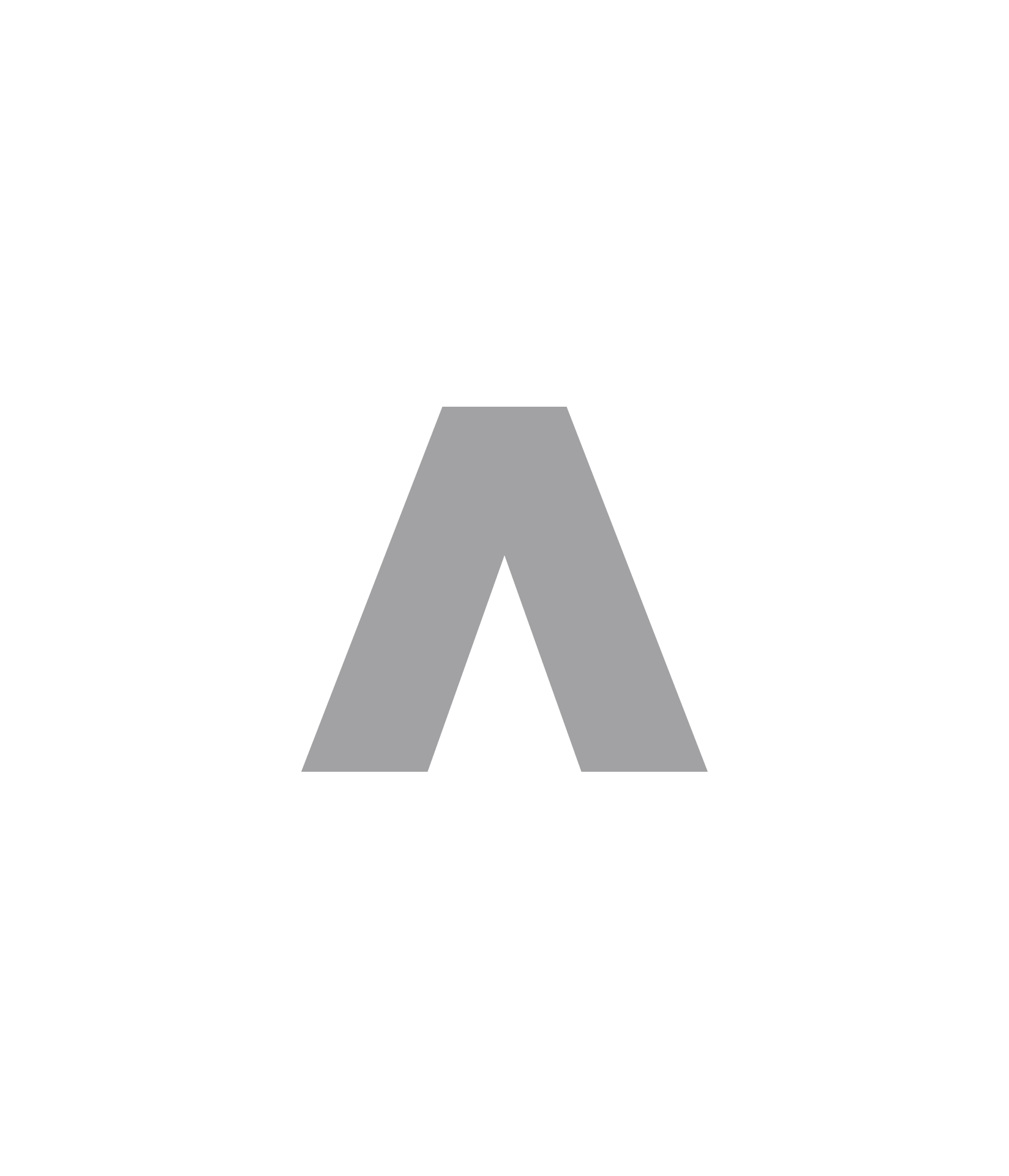