Ammann Plant Technology Protects Ultra-Eco Location
Ammann Plant Technology Protects Ultra-Eco Location
Lake Levico is in Italy but its beauty resembles that of a Norwegian fjord. Surrounded by the majestic Trentino Alto Adige mountains and thick forests, the emerald-green lake has walking paths for summer strolls and shady spots for fishing.
It is a true marvel of nature, as proven by the recent awarding of the prestigious Bandiera Blu eco-label, given for the lake’s outstanding water quality and overall environmental value.
Protecting such a gem is a must, which is why Edilpavimentazioni recently chose an Ammann plant with environmentally friendly features to operate at its nearby production site. The ABA 210 UniBatch Asphalt-Mixing Plant utilises Ammann technology to advance sustainability – including the RAH50 second-generation dryer and the new Blue Smoke Treatment (BST) capture system.
Edilpavimentazioni, a road construction company based in the province of Trento, has expanded impressively since its founding in 1985. Today, it has four asphalt production sites and 75 employees across the region. It handles essential asphalt production and roadbuilding projects at the regional, national and EU levels.
The company conducted a great deal of research before choosing the Ammann ABA UniBatch, and its decision paid immediate dividends. “At a functionality level, we noticed a change compared to the previous systems,” said Gianluca Viola, owner of Edilpavimentazioni. “The asphalt production is efficient, the material is mixed and processed perfectly.”
The dryer drum and its middle ring enable heating of the millings through contact with the aggregates. “Previously, we couldn’t do it because the milled material was inserted into the cold mixer,” Viola said. “The final result is a higher level of quality, and also energy savings and a reduction in emissions.”
Ammann’s advanced as1 Control System also added value. “It allows us to have real-time monitoring over all facets of production, such as bitumen consumption, energy consumption and the quality of the product itself,” Viola said.
Minimising blue smoke
Edilpavimentazioni eagerly included BST, one of Ammann’s newest sustainable solutions, in the purchase. BST intercepts fumes during truck loading and redirects them to a multi-stage filtration system. There, a patented solution leverages thermal forces to reduce energy absorption.
After filtering removes oily particles, the remaining gases are directed to the combustion chamber. This lessens fuel burn because the captured air is already heated. Sustainability is further advanced because condensed oil collected in the filter can be recycled.
The BST allows a constant flow rate to the chimney without increasing the gas stream. It requires no confinement equipment, is inexpensive to operate and can be installed on plants provided by Ammann or other manufacturers.
RAH50 2nd Gen.
The Ammann ABA UniBatch is equipped with the second-generation RAH50 dryer/drum, which utilises a ringed chamber to protect RAP from high flames. Sticking during discharge is prevented by new internal blading and a revamped evacuation system that does not require an internal elevator. The RAH50 2nd Gen. enables recycling of 50% RAP, which can increase to 60% when combined with Ammann’s cold recycling process.
This slow, general heating results in low volatile organic compound (VOC) emissions. It lowers CO2 emissions and energy consumption while protecting the RAP and even conserving the use of additives.
“We are producing normal and modified bitumen,” Viola said. “Furthermore, we are testing the production of warm mix through the use of Ammann Foam technology. We are achieving excellent results.”
Additional benefits
The Ammann ABA UniBatch is easily customisable, thanks to various technologies that meet the customers’ specific needs. Edilpavimentazioni chose a MIB 14.4 burner powered by LPG and compressed natural gas (CNG) that can also utilise heavy oil, resulting in significant savings in fuel costs.
Edilpavimentazioni has employed key features to ensure outstanding productivity, as well as reductions in odour, noise, dust and fumes. “The acoustic impact has improved, emissions have decreased, and the plant overall is performing better in many aspects,” Viola said.
Edilpavimentazioni realises that lowering emissions is crucial, but that alone is not enough.
“We are also using solutions to contain dust and drastically reduce noise,” said Rocco Viola, site and production manager of the Levico operation. “These are important features related to sensitive sites, such as Levico, that require a great deal of attention to environmentalism and tourism.”
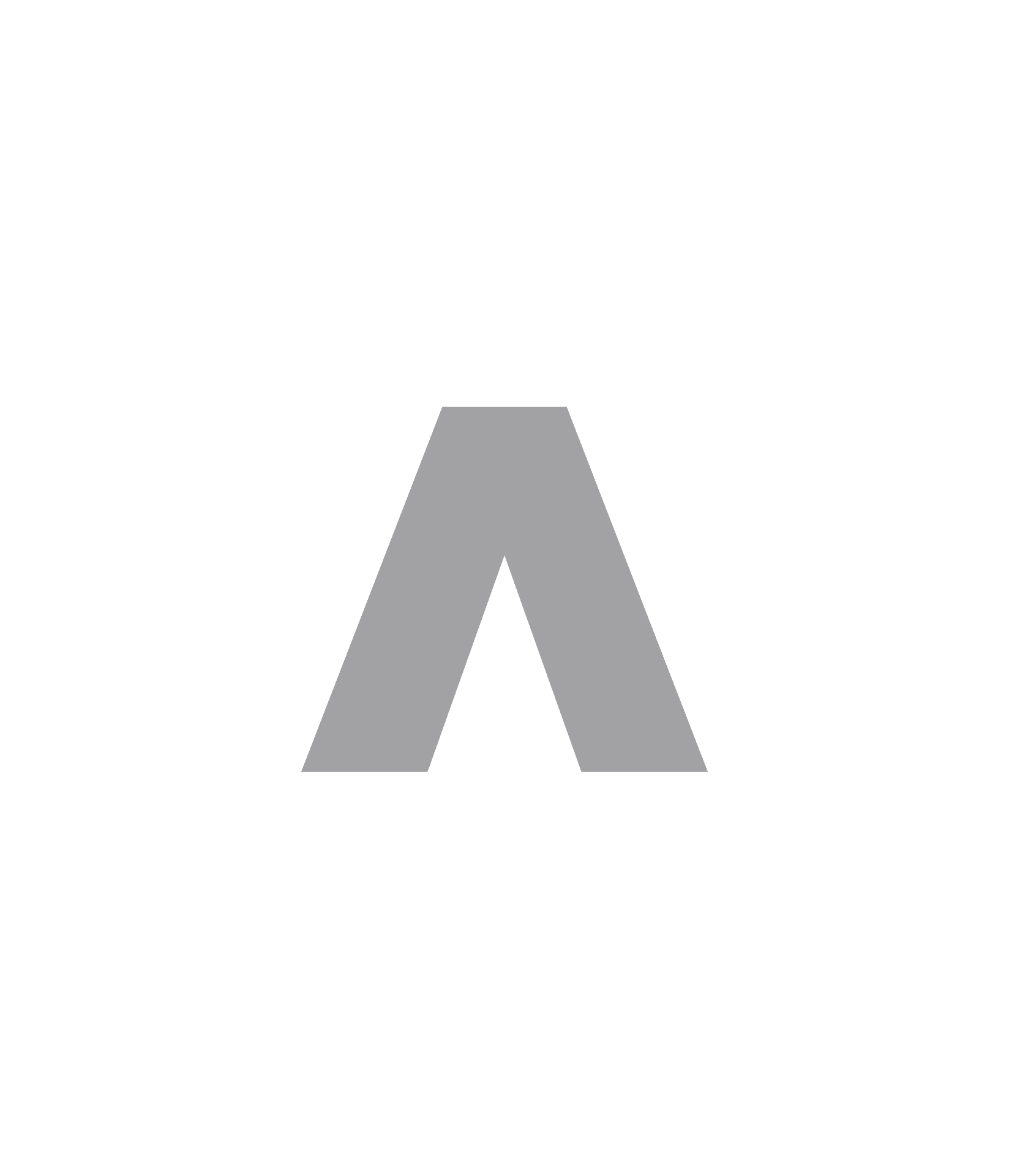
Formulário de Contato
Agendar uma reunião on-line
Entre em contato conosco para conhecer um representante de vendas perto de você
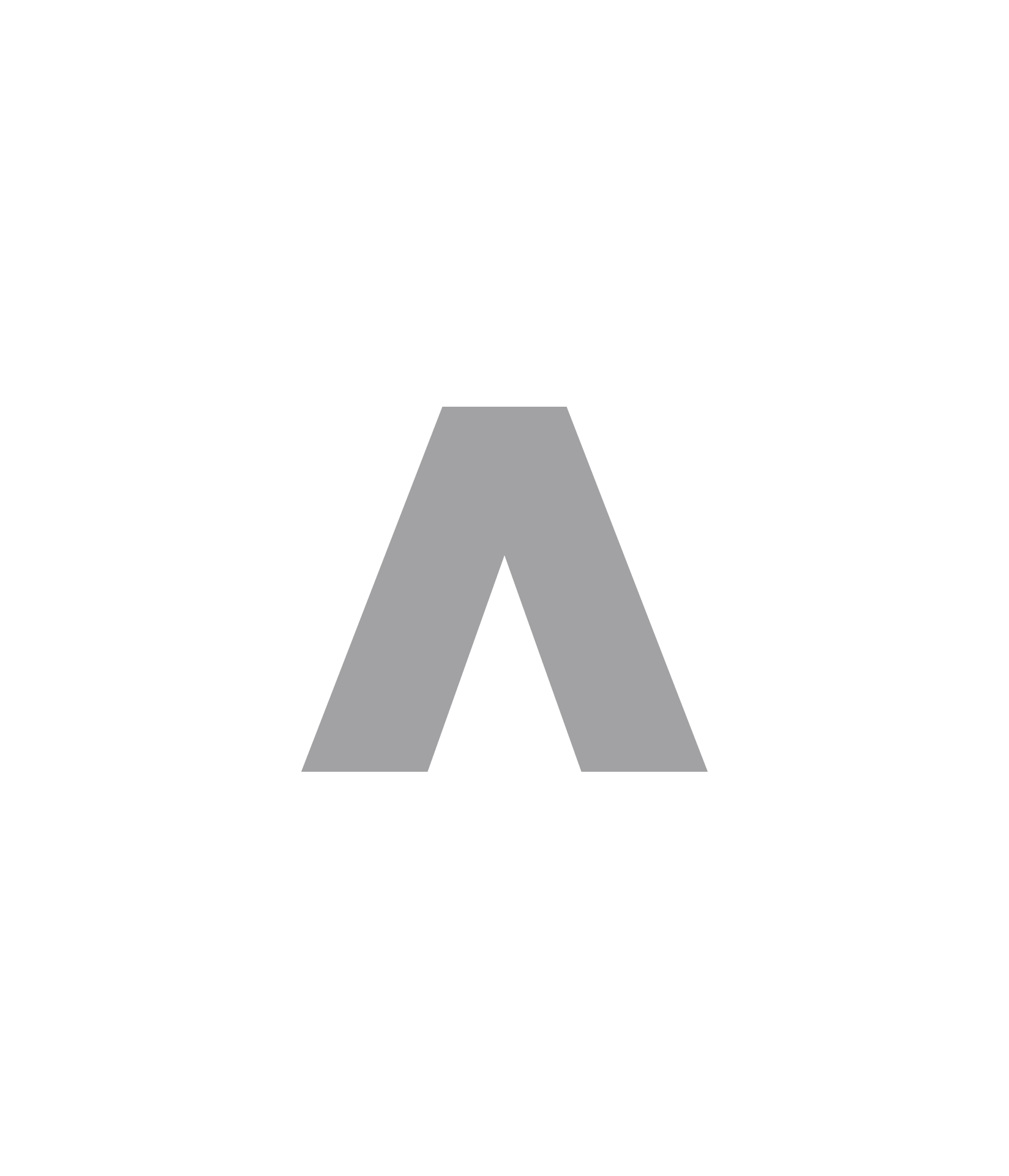